Solving the handover gap from construction to facilities management
Amr Raafat, Chief Innovation Officer at Windover Construction, recognized a serious gap in the construction handover process that he and his team sought to improve for their clients. Windover Construction, a general contractor with a focus on technical innovation in the New England area, serves commercial, healthcare, and educational clients such as Harvard University, Philips Exeter Academy, Endicott College and more. Amr knew Clients weren’t utilizing cumbersome manuals and PDF drawings, and even if a Revit file was provided to a client, the chances of an owner having a BIM expert on staff were slim, leaving most clients with unhelpful documentation for facility management.
As a standard practice Windover’s VDC team coordinated all projects throughout design and build phases with 90% accuracy. Despite following the best industry practices, they realized all their hard work and the valuable data created during the BIM coordination process was lost at client handover. Amr claimed, “The investment of time and effort the MEP and construction teams put in for the whole building right now stops after coordination.” Amr knew their clients could be using this lost data for facility management, but the information was lost in the contractual documentation they were providing. Windover sought a solution that would extend their technology to their clients, ideally incorporating their BIM data while being less technical.
The solution: Digital twins
The Windover Construction team discovered Autodesk Tandem, Autodesk’s digital twin solution. After some initial testing Amr and his team realized they could easily take their fully coordinated Navisworks models and use Autodesk Tandem to provide their clients with an accurate replica of their building that could also house facility management data. Amr explained, “Tandem offers to take BIM data one step further. With a little bit more dedication and creativity, our clients can leverage these user-friendly, information-rich, comprehensive models for many years to come to streamline communication and make it easier for them to navigate through the building services.”
Windover began building digital twins of their ongoing projects and upon completion they were handing over accurate replicas containing not only construction and design data, but also facility management data, such as warranties, installation dates, manufacturer information and much more to clients like Philips Exeter and Endicott. The VDC team saw Autodesk Tandem as a living digital document for clients, a way to curate project data that could evolve and still be used five to 10 years after construction.
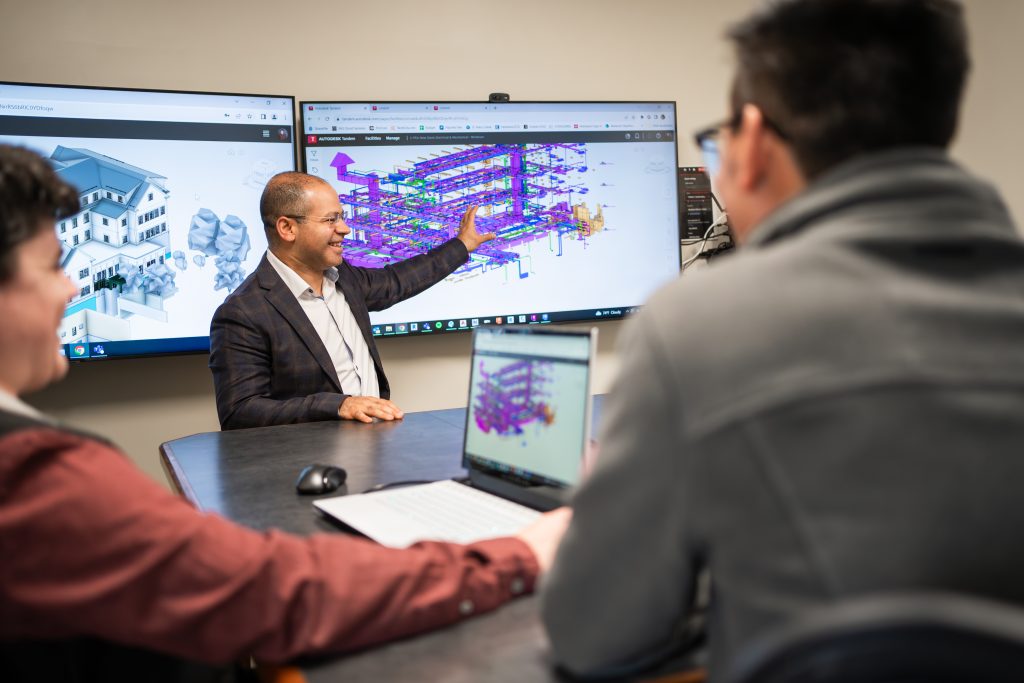
Building a digital twin
“It’s not as time consuming as most people would think,” Amr explained about creating a digital twin in Tandem, and that after all the time and effort they had already spent coordinating models, a digital twin deliverable became, “a no-brainer.”
Windover’s VDC team was already providing clients with laser scans prior to sheetrock and fully coordinating BIM models—so adding a digital twin to the mix was no complex feat. Their BIM coordination process consisted of taking Revit models and AutoCAD 3D files and coordinating all trades in Navisworks throughout the design and build phase. Since the team already put the effort into coordinating the model to 90-95% accuracy, importing it into Autodesk Tandem was a simple solution. From there, they would dedicate a VDC specialist to fill in the facility management data—taking about two weeks depending on the size of the project.
Not only was it a quick process, building a digital twin proved to be a repeatable process, that housed project data in a straightforward way. Classification systems could be tailored to their clients and repeated on each of their projects. Windover could easily document and link to all manufacturer information including warranties to assets—which their clients would be able to easily find by navigating to the item in the model and reviewing its properties. In addition to housing data in a user-friendly way, Windover also found they could customize saved views for their clients, meaning they have full control over helping their clients navigate to the information they deemed important with just a few clicks.
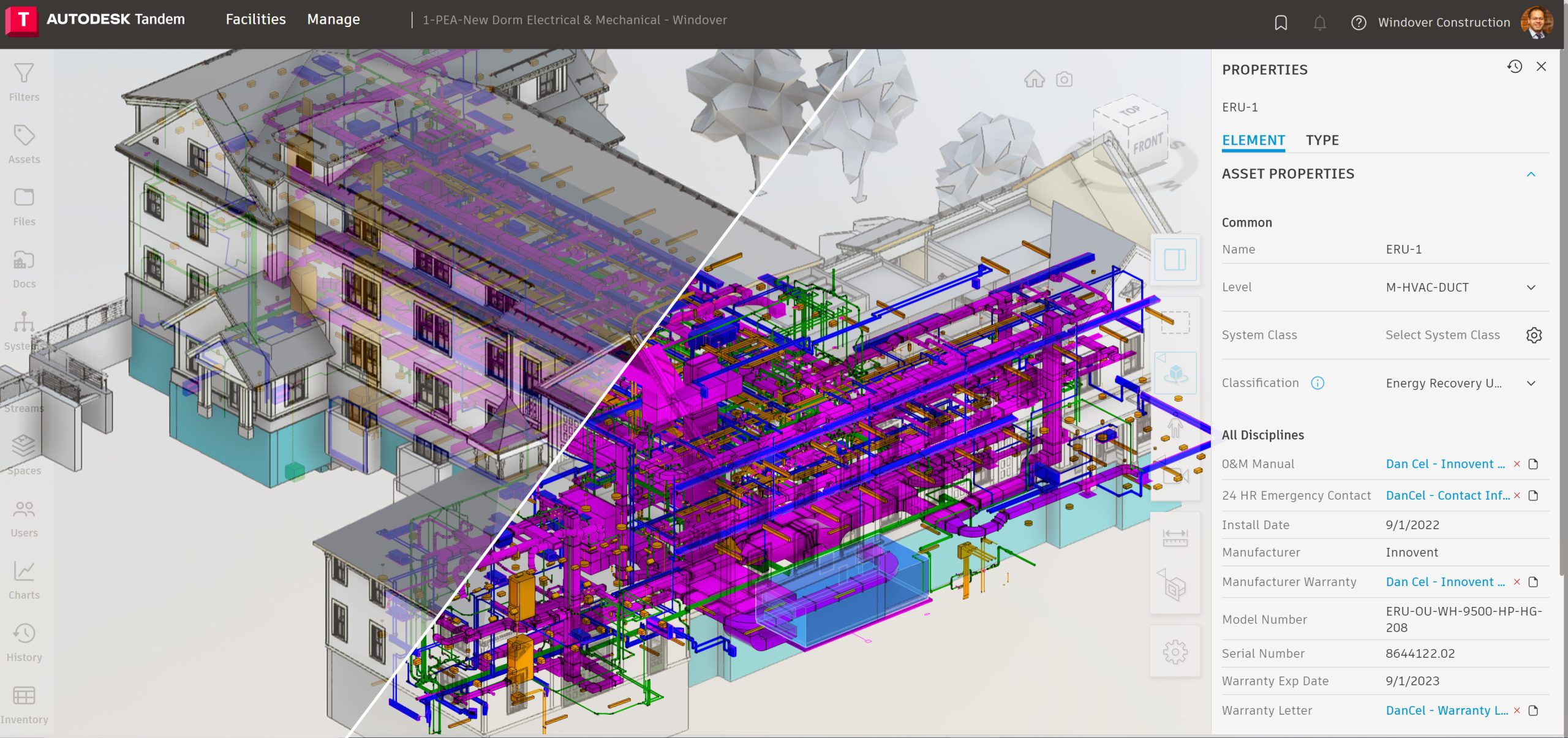
The handover
Amr and his team saw Autodesk Tandem as an opportunity to extend their BIM technology to their clients, without it requiring technical knowledge. Amr explained, “Tandem is offering us a great opportunity to provide value for the owner and facility managers who are not experts in BIM. Facility management teams aren’t expected to be experts in BIM like us, and that’s okay. But with a web-based link in Tandem you can go walk through a site. It is very easy.” Clients are able to visualize their buildings, data, and have a contextual reference at their fingertips. Autodesk Tandem eliminates the need for paper manuals, PDF drawings, or even walking the site to recall needed information. For instance, the use of Tandem will eliminate the need for QR codes—why go physically scan a QR code on a mechanical unit when you can navigate the accurate 3D replica and access the warranty in just a few clicks.
The new data-rich digital twin was a revelation for Technical Planner, Curtis Boivin, AIA, of Phillips Exeter Academy and his team. “Having a digital twin of a building is a real benefit to us. Not only can I identify the assets in the space, but those assets have operations manuals directly attached in Tandem. So rather than having a manual remotely someplace, the manual is wherever I am.” For more insight from Curtis, read the full story here.
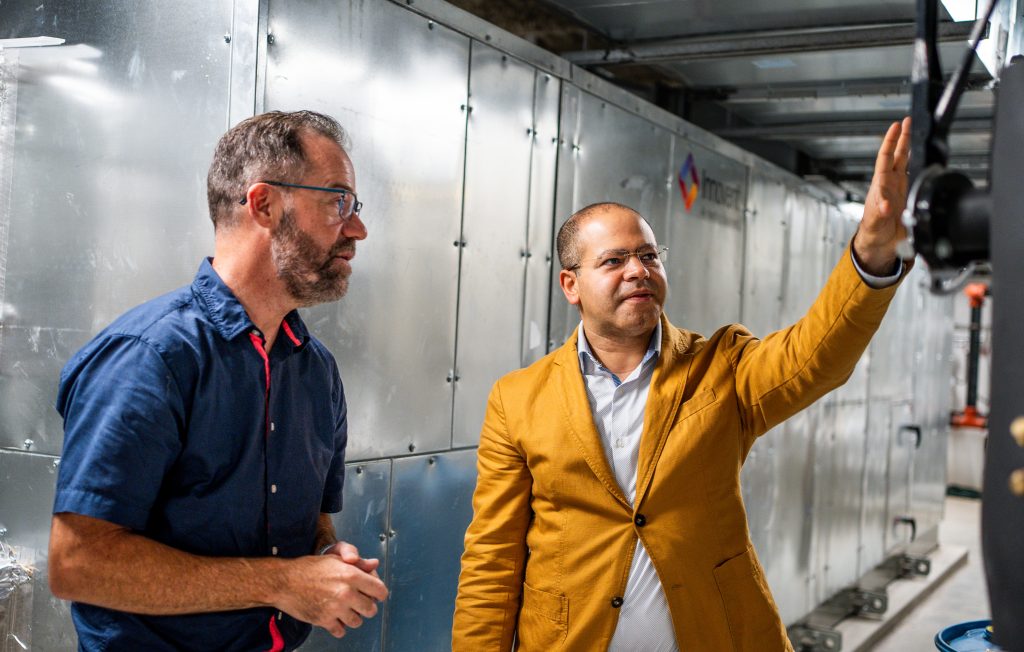
The future of digital twins for Windover and their clients
While the digital twin is operational today, we still can’t anticipate all future use cases as Tandem develops. Amr and his team expect the benefits of Tandem to have longevity, “The power of this is that it’s a living document. 10 years from now when replacing an air handling unit or lighting fixtures they can update this data and even add to it.” Beyond that, building owners and operators will have access and insight into building data like never before—the ability to see IoT sensors and even predictive analysis.
The response for Windover’s digital twin deliverable has been overwhelmingly positive. Clients appreciate the digital twin Tandem handover so much that Windover has decided to make it a standard part of their practice, even without a client request. It’s also led to new types of work for the Windover team—introducing scan-to-digital-twin requests from their clients for already constructed facilities.
Join the digital transformation and benefit from a digital twin
We’re here to support you in harnessing the power of digital twins for your business. Understanding the technology, its applicability, and your readiness to adapt to it is pivotal. That’s why we’ve crafted a comprehensive Digital Twin Assessment Readiness. It’s designed to provide you with an in-depth understanding of your readiness, highlighting potential compatibility with the integration of digital twins into your workflows. Start your journey now by accessing the Digital Twin Readiness Assessment.
More resources
Discover more articles, webinars, and whitepapers. Here are a few we think could be of interest.