The Charles H. Wright Museum’s digital transformation to becoming a ‘Smart Museum’
When sustainability efforts are discussed, consumers often look at the initiatives undertaken by major corporations to achieve these goals. Rarely do we consider the efforts of our local museums in striving to diminish their carbon footprint or embrace cutting-edge technologies for more eco-friendly building operations or implications to visitor experiences. Surprisingly, the collective number of museums in the United States surpasses that of many renowned retail and restaurant giants combined—amounting to an impressive 35,000 establishments. One institution, nestled in the heart of Detroit, is carving out its own unique path, by adopting new technology that will support its goal to be a “smart museum.”
In the pursuit of cultural preservation and community impact, the Charles H. Wright Museum of African American History in Detroit has undertaken a groundbreaking digital transformation, emerging as a “smart museum.” By integrating digital twin technology, the museum not only enhances its facility management but also pioneers a model for sustainability in cultural institutions nationwide. This transformative journey not only addresses the challenges faced by the museum—but also serves as a beacon. By urging other cultural institutions to embrace innovative technologies for sustainable practices, fostering collaborations, and making a tangible impact on both their mission and the environment.
Get to know one of the most important institutions in the United States: The Charles H. Wright Museum of African American History
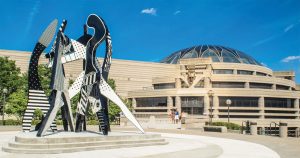
The exterior of the Charles H. Wright Museum in Detroit, MI.
“The Charles H. Wright Museum of African American History opens minds and changes lives through the exploration and celebration of African American history and culture,” shared Neil Barclay, the museum’s President and CEO. Engaging with an audience of hundreds of thousands annually, a significant portion are in-person visits from the Detroit Metro Region itself. The museum’s significance extends beyond its walls, as Neil emphasized, “the Wright Museum is one of 20 organizations that the Ford Foundation identified as one of America’s Cultural Treasures. In their view, if the museum did not exist, the culture landscape in the United States would be changed forever.”
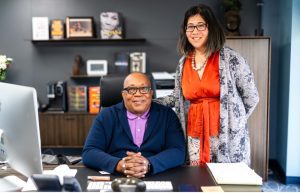
The Wright Museum President Neil Barclay, accompanied by CSO Leslie Tom.
The museum was founded in 1965 by Detroit obstetrician and gynecologist Dr. Charles H Wright with the goal of creating a space for “celebration and remembrance.” Chief Sustainability Officer and architectural designer, Leslie Tom shed light on the history of the 125,000 square-foot twenty-seven-year-old building (built in 1997). “It was designed by two Black Detroit architects, Howard Sims and Harold Varner. They designed this institution based on an African village. We have a huge 140-foot dome, and off that dome, that centering kind of village space offshoots our museum store, the theater, the exhibitions, and the classrooms below.” Leslie’s passion for the museum’s infrastructure is apparent, “it has become this beautiful iconic space within Detroit.”
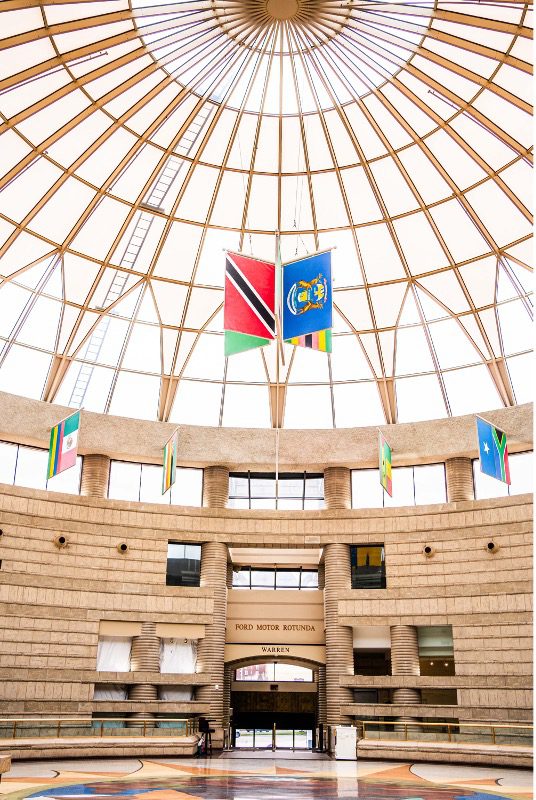
Inside the Rotunda of the Wright Museum.
The Wright Museum features a permanent exhibit that guides visitors through an immersive journey, encompassing walkthroughs of historical periods, art galleries, rotating exhibits, showcased sustainability projects, and a myriad of other enriching experiences. Going above and beyond the typical museum offerings, the dedicated curators and administrators orchestrate diverse programs to foster learning and engagement. These range from off-grid Earth Month concerts to elegant galas and a host of other engaging events.
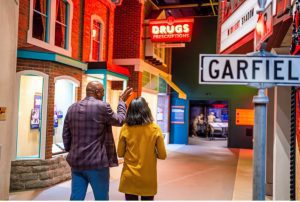
A glimpse into the complexity of one of the Wright’s exhibits taking visitors back in time.
The Wright’s impact and the ripple effects of a commitment to mission and community lay the foundation for a sustainability framework to highlight what museums do well, Leslie explains that as, “opportunities to expand the triple bottom line to be—people, planet, prosperity, and programs.” The triple bottom line is a concept for environmentally and socially conscious businesses or organizations to measure their impact beyond financials. Consequently, they have dedicated their efforts to developing initiatives that not only enhance the sustainability of their practices but also serve as educational tools. Ultimately, inspiring and encouraging their guests to actively participate and take meaningful actions.
A museum with deeply rooted responsibility in sustainability
“A lot of what is happening with our planet is really adversely affecting black and brown communities, even more so perhaps than the world at large,” explains President and CEO, Neil Barclay. The Wright Museum sees the institution as responsible for leading by example – knowing that minority groups are disproportionally affected by climate change globally, the museum sees it as their responsibility to educate and act accordingly.
Leslie draws on her architectural and information management background to approach the museum’s sustainability comprehensively, encompassing maintenance, operations, and renovations. Recognizing that the museum’s building represents one of the largest areas where they can make a significant impact on sustainability goals, Leslie is motivated by the World Green Building Council‘s assertion that 39% of carbon emissions stem from buildings, with 28% attributed to the operational phase, particularly in the efforts to regulate heating and cooling. With the ambitious objective of establishing and maintaining a sustainable building, Leslie actively sought innovative solutions to shape the museum into a “smart” and environmentally conscious institution.
The Wright Museum’s digital transformation
Creating a Smart Museum
The Wright sought to build a path towards becoming a smart museum by creating the ability to access, collect, and analyze operational data. A smart museum would allow the Wright to break down silos through the various departments, using software and data to drive continuous improvement for their staff, visitors, vendors and volunteers’ experiences, safety, health, and wellbeing. The Wright uses “Smart Museum” as the umbrella term for its three primary areas of focus: Smart Facilities Management, Smart Exhibitions, and Smart Sustainability. To collect the data necessary for a Smart Museum, the Wright would have to embark on a digital transformation, implementing new technologies and software to unlock the power and insights they wanted to achieve. To achieve their goals, they aimed to create a digital twin – a replica of their building that could provide insight to their operations for each sector of the smart museum.
The initial hurdle
The first hurdle the Wright encountered was a lack of documentation for their building and assets. Executive Vice President and COO, Jeff Anderson shared, “When I first arrived here in 2019, there weren’t any blueprints that we could count on a hundred percent.” Unfortunately, all the original drawings and AutoCAD files were lost in a fire at the architect’s office, leaving the Wright Museum with very little to no documentation.
Not only does the lack of documentation cause a hurdle for creating a smart museum, but it also impacts the efficiency of facility maintenance long-term. “You try to search and find information that either doesn’t exist, or you spend hours and hours trying to find information that’s just buried somewhere. It creates a lot of challenges, wastes a lot of time, and a lot of inefficiencies,” expressed Warren Emerson, Director of Facilities for the Wright Museum. The lack of proper documentation made capital planning, building maintenance, and plans to be sustainable difficult – posing hurdles for each sector of the institution. The Wright Museum would have to start their digital transformation from the ground up with a Scan-to-BIM-to-twin process.
From Scan to BIM
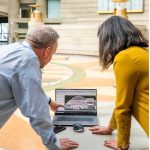
Leslie reviews the final BIM model of the facility that was created from the point cloud and turned into accurate geometry mirroring the museum using Autodesk Revit.
Eager to jump the initial hurdle, Leslie attempted to use traditional documentation methods to capture the data, with hand measurements. She quickly concluded that this methodology wouldn’t work for a complex 125,000 sq.ft. building with curved surfaces and hidden systems. Leslie said, “There’s so much geometry, especially the dome. I had to do the calculation to figure out there are seven degrees per single pane of glass in the dome—and to model that it was impossible, and so we brought in a 3D laser scan to be able to take all the geometry of this entire institution and then turn that into a Building Information Model (BIM).”
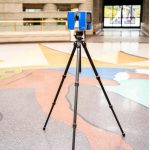
A laser scanner used to capture a point cloud of the Wright Museum.
The museum employed a scan to BIM technique, utilizing a laser scanner to meticulously capture a detailed point cloud of their facility. The Wright collaborated with their partner Charles Mclean of OM Green Group, leveraging Autodesk Recap to turn the point clouds and generate a mesh illustrating the building’s surfaces. This mesh served as the foundation for modeling the facility in Revit, providing the museum with both 2D plans for operational purposes and a comprehensive 3D model. The Revit model (also known as the BIM model) would serve as the foundation of the digital twin.
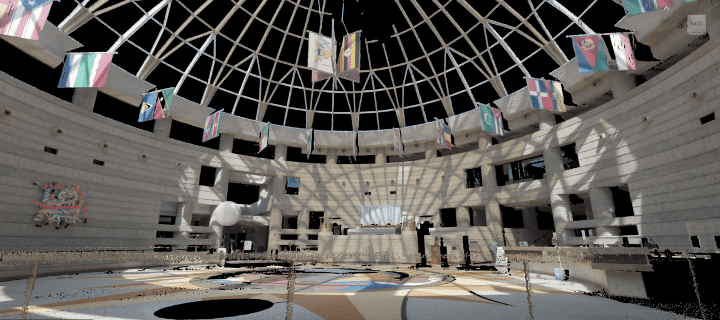
A point cloud with a photo overlay from laser scanning.
What is a digital twin?
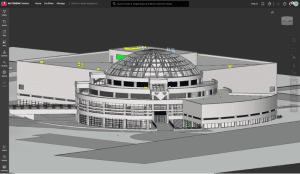
An exterior view of the digital twin of the Wright Museum using Autodesk Tandem
A digital twin is a highly accurate replica of a built facility with data associated with the assets and systems, as well as the ability to connect to Internet of Things (IoT) sensors. While digital twins are built with BIM data, they lower the barrier to entry for users that are not as technical. Giving them the ability to easily understand their building, assets, and systems through power to search for specific information or assets, as well as the ability to save views. The value in a digital twin resides in the data, allowing building managers to maintain facilities more efficiently, providing sustainability officers quick insights into live building performance, and giving owners quick insights into cost estimates, space usage, and more.
From scan to BIM to digital twin
After the Revit model is created the heavy lifting is already done. Autodesk Tandem ingests Revit models and uses geometry for the base of the digital twin. From there, the museum and partners can classify assets and link them all to their facility management data (warranty information, serial numbers, O&M manuals and maintenance plans). This first step would assist in quickly addressing problems for their facility maintenance team – they would no longer have to waste time searching for documentation. Instead, they’d be able to find the asset quickly in the digital twin and all the associated information.
The integration Sensors + Feedback
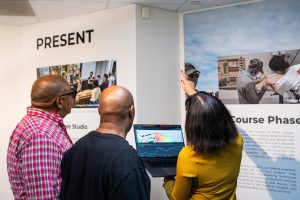
(Leslie, Warren and Jay, building engineer in a gallery pointing to a CO2 sensors that is feeding near real-time data into Autodesk Tandem.)
After the creation of the twin in Tandem, the Wright sought to use as much data as possible to improve their operations so they began to integrate the use of IoT Sensors – collecting and visualizing near real-time data would solve that need. Autodesk Tandem can ingest data from IoT sensors allowing the museum to measure, track and document an endless array of inputs. The Wright Museum’s initial pilot with sensors is measuring CO2, humidity, temperature, and proximity. Leslie explained that with the IoT sensors “our data is getting fed back to us and we can start to be proactive about our policies, about how we’re going to take care of our building, and any future building system decisions that we want to start to analyze.”
Using a digital twin and IoT data
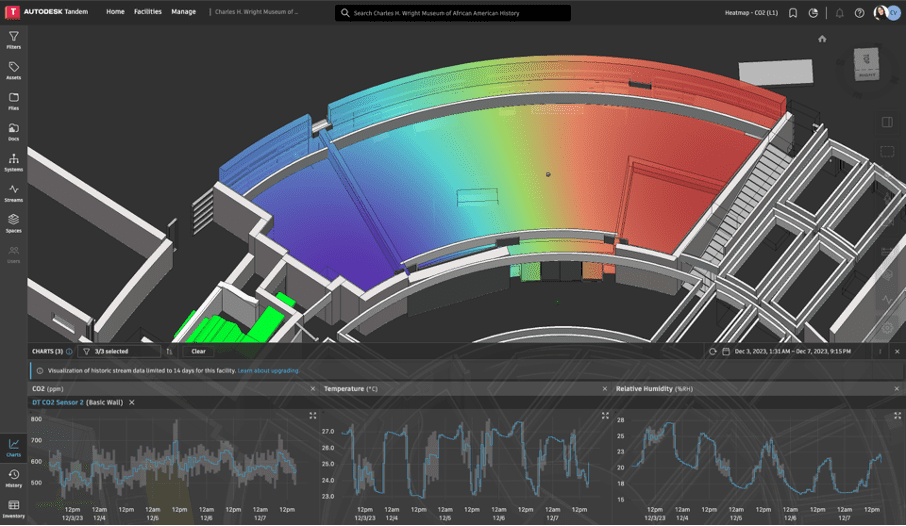
Inside Autodesk Tandem we see one of the Wright Museums galleries with a heatmap illustrating the CO2 levels and three times series charts showcasing CO2, Temperature, and Relative Humidity.
The Wright Museum started to explore their data within Autodesk Tandem in two primary ways: charts and heatmaps. First, the times series charts can log and display data taken up to once every minute— giving users a granular and holistic way to understand what’s happening with their systems or sensors. Second, the heatmaps overlay that data to the 3D model, either by applying the information to the spaces or building systems. This gives the museum the ability to contextually visualize or analyze the data within the building.
Finding value in operating a Smart Museum: Smart Facilities Management, Smart Sustainability, and Smart Exhibits
Improving the Wright Museum’s Smart Facility maintenance process with a digital twin
More effective facility data management
“We’re trying to get away from so much time being wasted looking for answers to questions that it would be nice to have an all-in-one central place and location. There’s only so many hours in a day, and I hate to spend a third of my day looking for things that don’t exist,” explains Warren. The Wright Museum is not alone – the International Facility Management Association (IFMA) recently released a research report that found that the average facility manager wastes up to 12% of their time due to fragmented data – some reporting even higher numbers of wasted time.
For other facility managers, regardless of the building type, their data was often siloed, incomplete, and in formats that were inefficient or not user-friendly. For example, most of Warren’s previous workflow was based on phone calls, emails, shuffling through PDFs, paper documents, and spreadsheets. With the new technology in place, the information Warren needs to operate a smart museum is easy and quick to find, “We can have it all in one system, at our desktop, at our fingertips, to answer questions effectively, respond to issues quickly—and everyone can have a great, wonderful experience here at the Wright Museum,” says Warren.
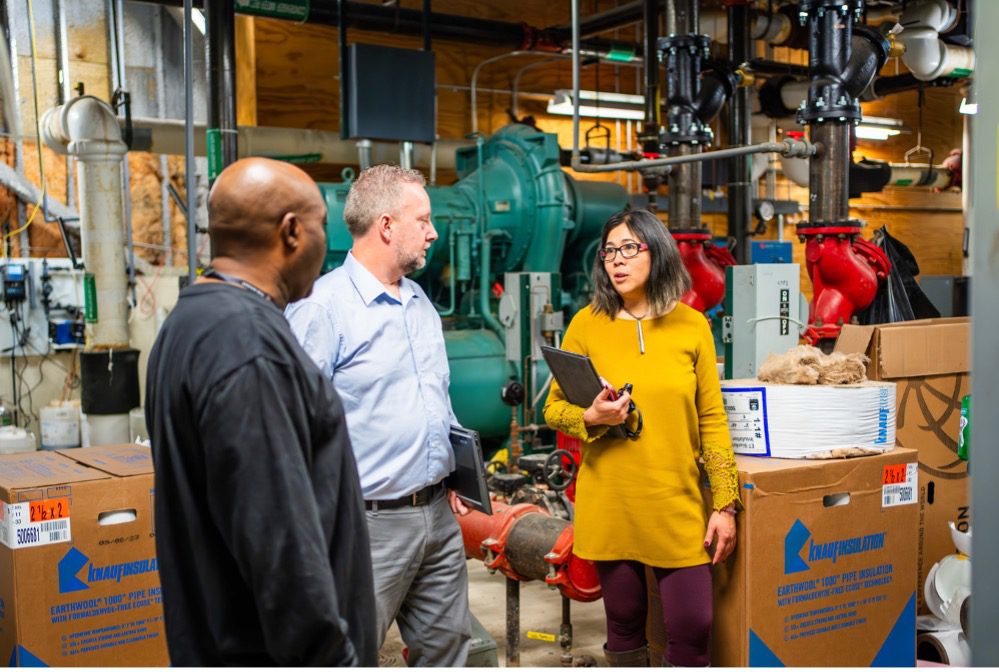
Leslie and technical team inside one of the large mechanical rooms that power the Wright Museum.
Entering the era of Smart museums proactive smart facility maintenance
“If we’re proactive in our approach, there’s not so much reactionary issues and problems,” explains Warren, “So we’re looking for Autodesk Tandem and Eptura to assist us in preventative maintenance, so we don’t have issues with deferred maintenance.” The Wright, just like other cultural institutions across the nation, are subjected to deferred maintenance – sometimes an almost unavoidable situation. Unfortunately, building operators generally can’t predict when equipment will fail – leading them to have to wait to repair their assets until they can receive the proper funding. “Deferred maintenance costs money, costs time, and just puts a lot of extra unneeded stress on the building and its components.”
With their digital twin, the Wright is working to predict when a mechanical system is out of operational thresholds and organize their inventory so that they can either proactively fix the issue or receive the funding needed. Connecting Building Management Systems (BMS) to Tandem, as well as other IoT sensors, could give both holistic and granular insights on their building’s performance. This gives the facilities team the power to make educated decisions ahead of potential turmoil.
“When we think about our systems in the long term, if we would not be doing proactive maintenance, we would be reactive all the time, and it just seems like it’s a missed opportunity not to be able to leverage this data and these resources that we have that represent this entire institution digitally.” From a sustainability standpoint, Leslie said, “Tandem allows us to be able to do analysis work with these different systems to do projections into the future of what equipment we want to use and how we can lower our carbon footprint from the get-go.”
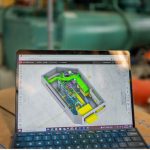
A digital twin of one of the large and complex mechanical rooms of the Wright Museum.
Budgeting beyond repairs
“Our investment in the technology, the BIM model, digital twin, those types of technologies, we are hoping that it will help us plan not only currently, but also for the future. We’re always looking at the budgets and the comparisons, the revenue coming in and what’s going out the door. I think that having the technology will allow us to be able to pinpoint more of what those costs are,” explained Jeff. With the insights from Autodesk Tandem, the Wright Museum expects it will begin to not only understand their building better, but also use their insights for capital planning, space management, and much more.
Protecting historical artifacts
More goes into operating and maintaining a museum than meets the eye, Warren explains, “Artifacts are very sensitive to temperature, very sensitive to humidity. It’s important that we have a system in place to track and monitor humidity. The last thing we want is for an exhibit or an artifact to be compromised because of inefficiencies in our systems. Autodesk Tandem will assist us in preventing issues within our system.” The museum has also extended this use case to monitoring leaks, hoping to protect their artifacts and facility from the possibility of floods using IoT sensors detecting moisture.
A new era of Smart Sustainability:
Operating a museum sustainably
“We’ve lived in a consumer based and disposable society for so long, one needs to approach sustainability through systems thinking and culture shifts”, Leslie Tom, reflects. By leveraging our digital twin technology stack, we are starting to save time across our museum’s departments to increase our capacity. We have more time to integrate sustainability into our data framework, collaborate across departments, and to implement processes, workflows, and policies.” The data that the Wright Museum has leveraged from their digital twin allows them not only to break down silos, but to create sustainable solutions explains Leslie, “Utilizing computation, we embed climate actions into our infrastructure, leveraging technology to enhance efficiency and innovation. Tandem data helps break down silos, offering immediate feedback for co-creating sustainable solutions, from exhibit design to facilities management with sensors enhancing our operational monitoring.”
Leslie continued to explain, “As we start to make more sense of what data is helpful and necessary, I anticipate all our departments will want more reports on our carbon emission numbers for exhibitions and events. We can collectively start to close the loop with pre-heating and pre-cooling spaces as we already know how many people are planned to enter our spaces. We are also planning to upgrade to a new Building Management System (BMS). This will allow for much more refined setpoints and zones in how we are using the museum. We can experiment on how to become a greener museum and with access to so much data; test our assumptions.”
Educating the public through “making the invisible visible.”
The Wright Museum is actively, “dedicated to climate justice, and is at the forefront of worldwide museums in its effort to make the invisible work of sustainability visible, so that everyone can see they have a stake in – and can contribute to – environmental preservation.” Often, sustainability issues are inconspicuous, so educating others on the subject may have hurdles – especially when it comes to proving how a building’s operation may be impacting the environment. Leslie sees the use of digital twin technology as a potential way to educate museum visitors about this topic.
Creating Smart Exhibitions
Design, Fabrication and UX Research
“A Smart Exhibition encompasses how we can leverage digital twin and sensor data through the entire design, and archival / virtual reality aspects of our exhibitions. There are perpetual opportunities for visualization with decision makers, artists, funders, etc. And opportunities to leverage data inputs and outputs for our exhibits,” explains Korzell Coe, architectural designer and assistant exhibition designer, who is helping to lead the Wright’s Smart Museum initiatives to leverage the digital twin model with design, fabrication, and visitor experience.
The potential to produce better exhibits with sensors
The Wright discovered they could use Autodesk Tandem to track guest engagement with a carbon dioxide sensor pilot. The CO2 sensors measure carbon dioxide exhaled by patrons in exhibits, while maintaining privacy, with goals to improve their exhibit installations, to better protect their precious artifacts, and collaborate more effectively with other museum departments. “We are using carbon dioxide sensors to be able to understand how many people are staying and lingering in different spots of our exhibition,” explained Leslie. Korzell commented they could track the data from these sensors visually in Autodesk Tandem to understand how patrons are moving and lingering in the gallery without taking invasive information. “This is providing valuable feedback for curators, almost like A-B testing. We can start to have near real-time feedback to understand how often people linger at our various interactive exhibition panels.”
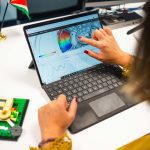
Leslie viewing a gallery’s CO2 levels via heatmaps inside Autodesk Tandem.
Calling other institutions to lean into technology
Through their digital transformation and the use of digital twin technology, the team at the Wright Museum is starting to see how impactful this transformation has been to their mission, sustainability goals, operations, capital planning, budgeting and more. There’s power behind data and releasing that data from siloes allows it to be valuable to more team members and opens the door to previously unimaginable collaborations between teams. By diving into new technology, The Wright has found how data can help them better propel their mission – and make their actions more visible to our internal workflows, visitors, and donors.
If museums across the nation were to adopt advanced sustainability practices, we could potentially see a huge shift in behaviors across many other industries – as museums are often trusted and influential establishments. The Wright Museum continues to establish itself as a thought leader for other cultural institutions. As a leader in digital twin technologies, Jeff advises, “When it comes to giving advice to other cultural institutions—do not be afraid to take risks.”
Taking the lessons learned from the Wright Museum, other cultural institutions can lean into new technology and find ways to reach their sustainability goals while simultaneously impacting multiple internal departments for the better. Leslie claims, “Our buildings, spaces, artifacts, and visitor, vendor, volunteer, and staff experiences are connected to data. The digital twin stacks can help to unlock collaborations and transparency.” She continues to call her fellow institutions to join the Wright Museum through their digital transformation, “there are approximately 35,000 museums across the United States, are also practicing these environmentally sustainable practices, we can really start to call for climate actions within our individual communities and regions.”
More resources
Discover more articles, webinars, and whitepapers. Here are a few we think could be of interest.