How facility management will improve in 2023
The challenges in facility management
The facility management industry faces many challenges due to the complexity of managing a broad range of services – from data management to sustainability. Facility managers must decipher an abundance of data in a variety of formats, spread across PDFs, printed documents, and disconnected facility management systems. The variety of formats makes it difficult to find, sort, or might not even be up-to-date information. This industry also faces growing demands for sustainability and environmental responsibility. It can be difficult to align the interests of different stakeholders, such as management, tenants, and investors, when it comes to best practices. However, the implementation of such solutions can be costly, and not all companies are ready to invest in them despite business drivers like tenant satisfaction, reporting, and compliance requirements.
Despite the hurdles in the facility management industry, the rise of new technology is beginning to make the jobs of building operators more efficient and sustainable. Digital twin solutions are creating integrations that make the building data for operations more digestible and easier to find, navigate, and update. This emerging technology is helping facility managers make more informed decisions, improve their sustainability practices, and overall be more operationally efficient.
What is facility management?
Facility management refers to the comprehensive administration of physical spaces and infrastructure within an organization or a facility. It encompasses a wide range of activities aimed at ensuring the optimal functionality, efficiency, and safety of a building. Facility management involves the coordination and supervision of various essential services—like maintenance and repairs, security, cleaning, waste management, space planning, and environmental sustainability. The primary goal of facility management is to create and maintain a productive, comfortable, and sustainable environment that supports the core objectives of its occupants. It requires a multidisciplinary approach, involving professionals with expertise in areas such as engineering, architecture, construction, project management, and operations. Effective facility management boosts operational efficiency, reduces costs, and improves the overall well-being and satisfaction of occupants and visitors.
For more resources on facility management, visit the International Facility Manager Association.
How will digital twin technology transform Facility Management in 2023?
Before we dive into how digital twins are going to transform the landscape for facilities maintenance, we need to understand exactly what they are. A digital twin for facility maintenance is a virtual model of a physical asset, such as an office building, that incorporates near real-time data as well as operation and maintenance data all in one place. It enables facility managers to monitor building health, make informed maintenance decisions, and optimize maintenance strategies. Digital twins facilitate remote collaboration, support the entire asset lifecycle, and provide a data-driven approach to improving facility performance and efficiency. Autodesk Tandem is a digital twin solution that is transforming how facility managers operate day to day; here’s how it could impact you:
1. Facility Managers can find information faster than ever before
For most facility managers (FMs), finding operation and maintenance data can take up valuable time, especially when overseeing multiple facilities like college campuses, municipalities, or commercial owners. A technician responding to a service request may need more information like asset manufacturer, warranty, serial number, and the upstream and downstream assets or rooms that may be impacted. To get this pertinent information, they may need to refer to multiple unrelated documents —that are potentially outdated, inaccurate, or might not even exist!
Autodesk Tandem is a repository for facility management information with the ability to store customized data for all components of a facility. Building operators can access the operations and maintenance manuals, asset information, websites, and any other documentation or linked resources for every asset that makes up the building. A digital twin can also improve the efficiency of field calls without the need to be directly on-site — like when a tenant reaches out about a broken mechanical unit and the facility manager can quickly access documentation and current operating conditions immediately in Autodesk Tandem.
2. Facility Management data can be associated with a 3D replica
Have you ever had a hard time determining what asset you’re looking at and if you have the correct information for it? A primary benefit of the digital twin is that it provides a 3D context for the assets, spaces, and systems – meaning every asset in your facility is visible, and the operations, maintenance, and performance information is tagged and connected to that asset. This provides a convenient visual context for both finding the information you need quickly and validating whether you have the right information.
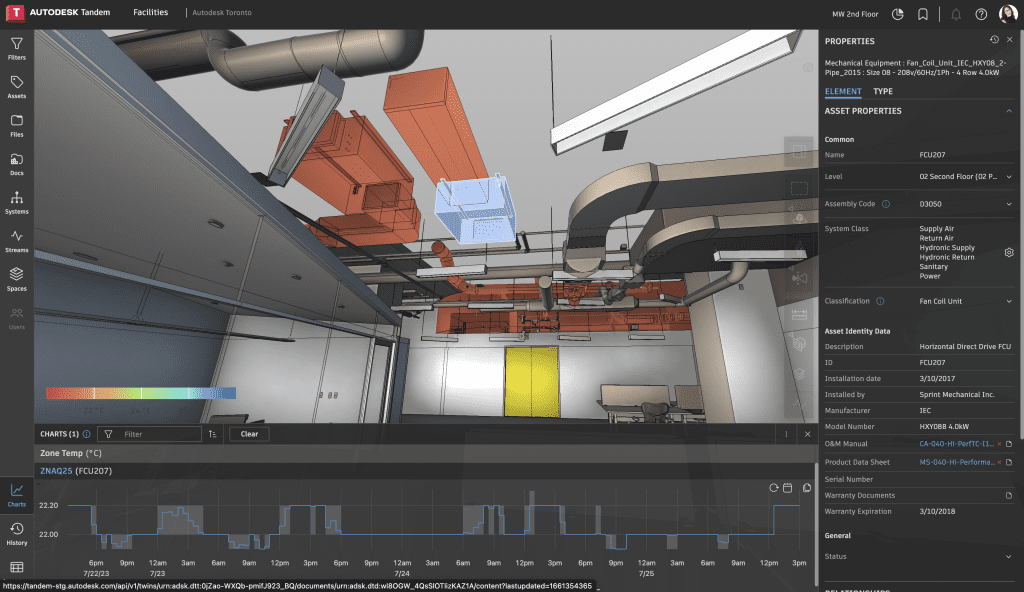
3. Facility Management data becomes easy to keep up to date
A common complaint from building managers is that they don’t have a convenient way to log new asset information. They will go to look up details about an asset and someone else will have handwritten the new serial number illegibly or it’s not up to date. Since Tandem is a data repository, it is quick and easy to modify information as needed, like as simple as updating an Excel spreadsheet – but with the extra benefits of the contextual 3D replica and a full history of every change. The digital twin allows your team to stay organized and informed while reducing the burden of synchronous communication.
4. Facility managers can better interpret a building’s complex network of systems
Let’s face it, not every building operator will have extensive expertise in understanding 2D building documentation, architectural concepts, or construction software—and that’s perfectly acceptable. Even the basics of locating the path of a building’s mechanical, electrical or plumbing system can be hard, with or without drawings, half of it is behind walls. Autodesk Tandem provides the ability to map the physical network of a system so facility managers can better understand the function, where they interconnect, and where they are located in a given facility. This can help take the guesswork out of what valve to turn off in an emergency or what rooms you’ll be impacting during a shutdown. Understanding your building’s systems ensures you can make informed decisions fast.
5. BMS data will have visual context
Data from your Building Management System (BMS) isn’t new – but giving it visual context is. Autodesk Tandem can ingest BMS data and provide you with in-context visualization of the heating, ventilation, air-conditioning (HVAC) and more. Near real-time data can provide Facility Managers with visual updates on occupant comfort and let them know how their systems are performing. Utilizing heatmaps overlayed on spaces or systems allows better insight into the building’s performance.
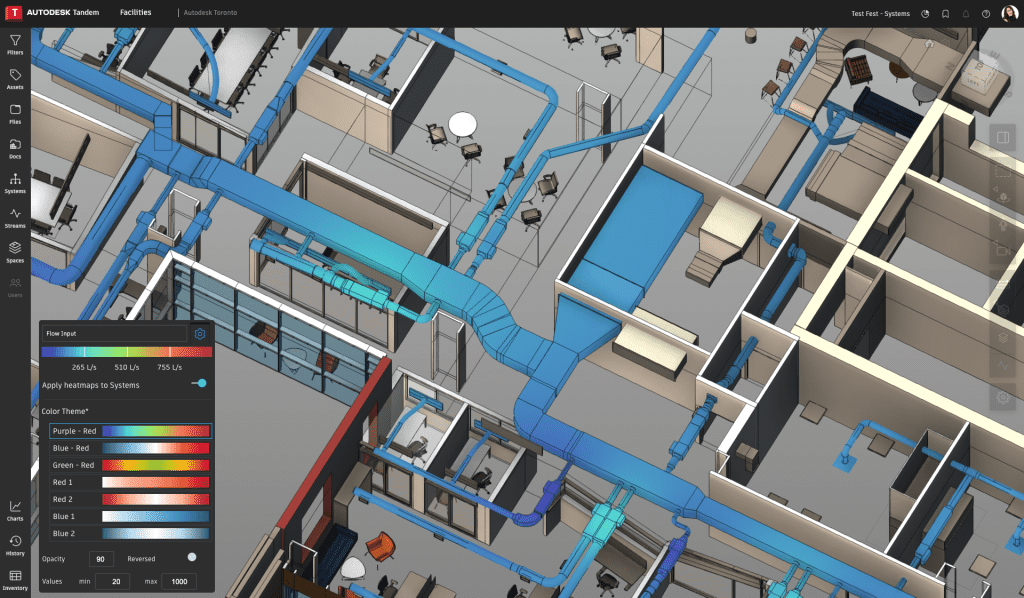
6. IoT sensors will unlock new insights for sustainable facility management
IoT (Internet of Things) integrations and possible use cases with digital twins are endless. As of right now, common IoT systems in buildings focus on occupancy tracking, energy management, or indoor air quality. Although the data supports better decision-making and sustainable choices, the IoT systems are often siloed offerings with stand-alone interfaces. To keep your building operating at optimal performance, while tackling energy and CO2 reduction targets, incorporating IoT data into a digital twin allows for cross-referencing and correlation in real-time — but without the overhead of data extraction and normalization each time a decision must be made.
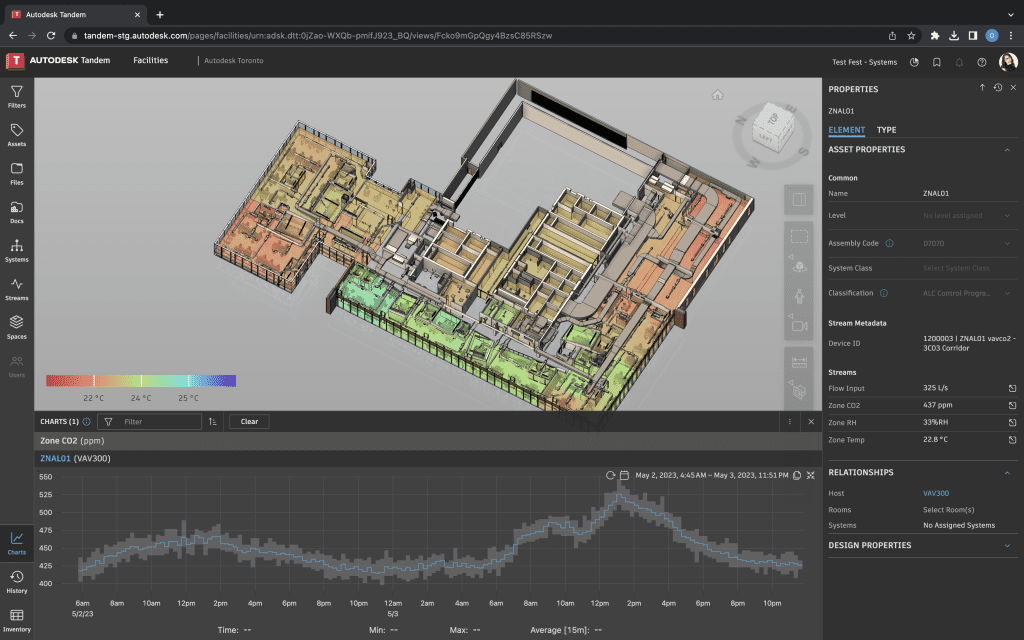
7. Preventative Maintenance will become more attainable
Data being fed from the IoT sensors to Autodesk Tandem helps facility managers find equipment issues before they turn into failures – keeping their facilities up and running and comfortable for tenants. With the help of heatmaps and charts connected to IoT sensors or a BMS, a facility manager could easily discover a fan coil unit is beginning to fail. This could be due to deviations in the heating or cooling of a room over time—indicating that the unit needs repair or replacement. These sensor integrations offer insight to avoid a unit from being completely non-functional, ultimately causing occupant distress and reactive maintenance.
Are you ready to speed up and digitize your facility management operations with Autodesk Tandem? Find information faster, access 3D replicas, easily update data, understand building systems, visualize BMS data, unlock IoT insights, and enable preventative maintenance? Learn more about transformative facility management here.
More resources
Discover more articles, webinars, and whitepapers. Here are a few we think could be of interest.