Extending Data to Facilities Management: How Phillips Exeter Academy is leveraging digital twin technology
In the heart of New Hampshire, nestled within the historic campus of Phillips Exeter Academy, a revolution in facilities management is quietly taking place. The academy, renowned for its rich educational legacy, encountered a common challenge in facilities management – the building operations team suffered from a highly fragmented workflow that was costly and inefficient when trying to maintain and operate both new and 200-year-old buildings. The facility management team knew they lost time searching for data to maintain their buildings as they sifted through paper plans and spreadsheets.
The challenge with fragmented facility maintenance workflows
The facility maintenance team often grappled with the little data they had for old and new buildings alike. “The challenge for running a facility in the modern age is that we have buildings that are 200 years old plus,” Technical Planner, Curtis Boivin, AIA, mused, standing inside a small room with tattered old blueprints for each building. “We have things that are built with older methods. And it’s very difficult to understand all the systems of the building quickly.” The facility management workflow for Phillips Exeter, and across the industry as a whole, is highly fragmented for both old and new buildings. An astonishing 95% of data is lost at construction handover, leaving building owners with very little knowledge about their building’s inner-workings—making it difficult to maintain and fix them efficiently.
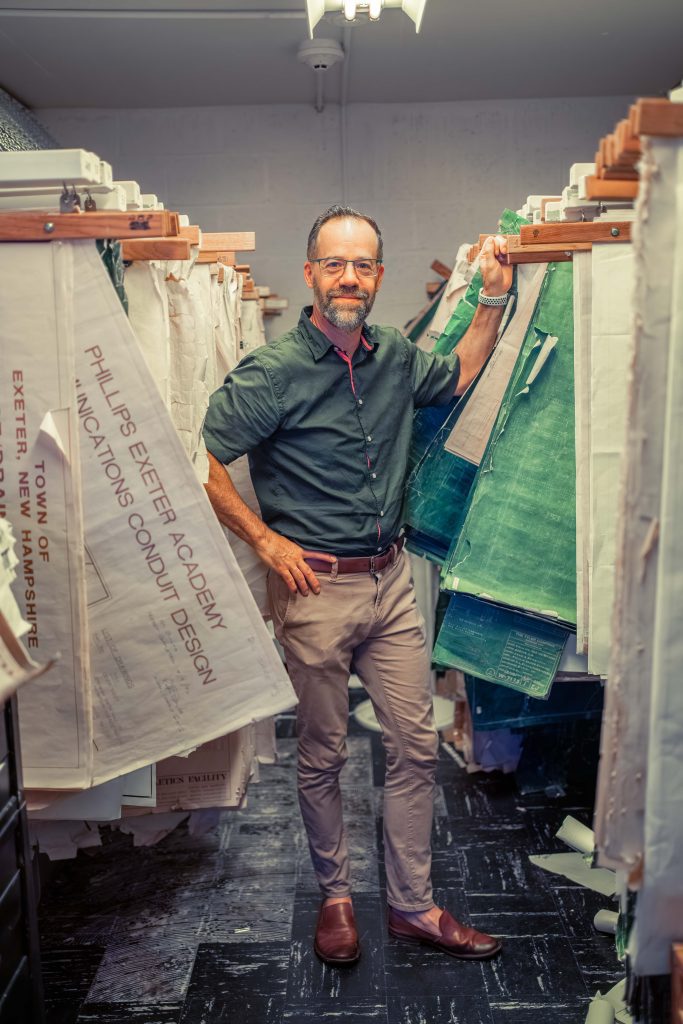
Fixing the data drop-off
That’s when Windover Construction stepped in with a new and innovative solution – a digital twin of Phillips Exeter’s new dormitory upon project handover. A digital twin is a data-rich, interactive replica that mirrors the existing building in appearance and substance. The digital twin provides a 3D model of the new building and contains maintenance data for each asset. So, for the first time, the facilities team at the academy could quickly find warranties, serial numbers, and any information they needed without shuffling through plans and PDFs.
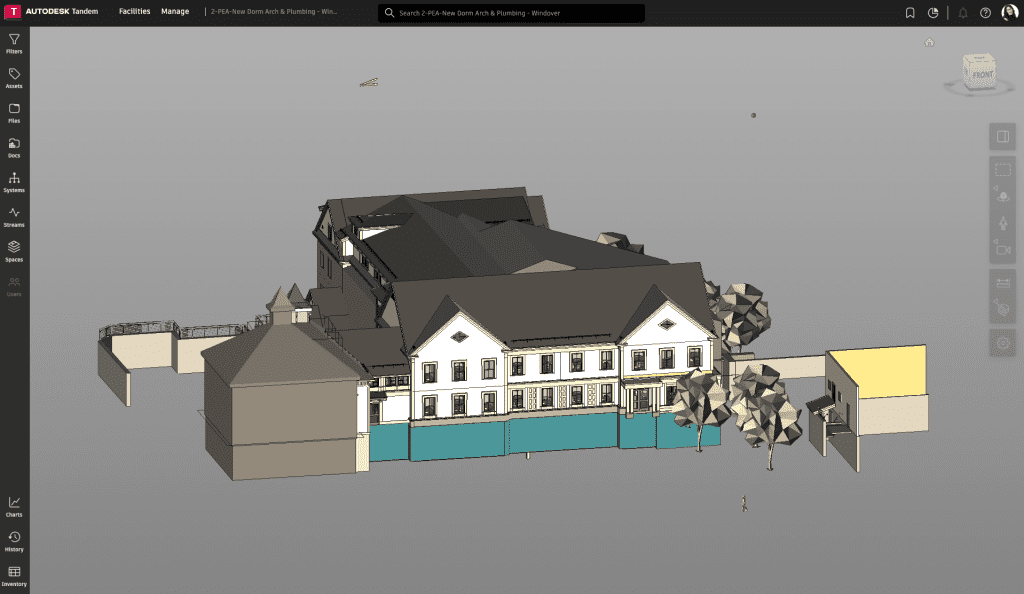
The value of a digital twin for facility management
The new data-rich digital twin was a revelation for Curtis and his team. “Having a digital twin of a building is a real benefit to us. Not only can I identify the assets in the space, but those assets have operations manuals directly attached in Tandem. So rather than having a manual remotely someplace, the manual is wherever I am.”
With Tandem, Curtis could effortlessly locate critical systems, trace pipelines through walls, and identify shutoffs without searching through mountains of siloed sources such as spreadsheets, PDFs, and blueprints. “You can see how systems are connected, where the shutoffs are…The real-time savings with Tandem is to find the information that you need to know quickly, to be able to repair things, to bring them up to operating standards fast,” Curtis emphasized.
The transition from traditional handover documentation to a digital twin was seamless, thanks to Windover Construction’s expertise. “The handover gap in construction has always been a problem,” noted Curtis. “A digital twin makes it so that there’s an accurate roadmap with precise information. So that in the future we know exactly what the problems are with the building as they happen, and then we can correct them and better maintain the buildings faster.”
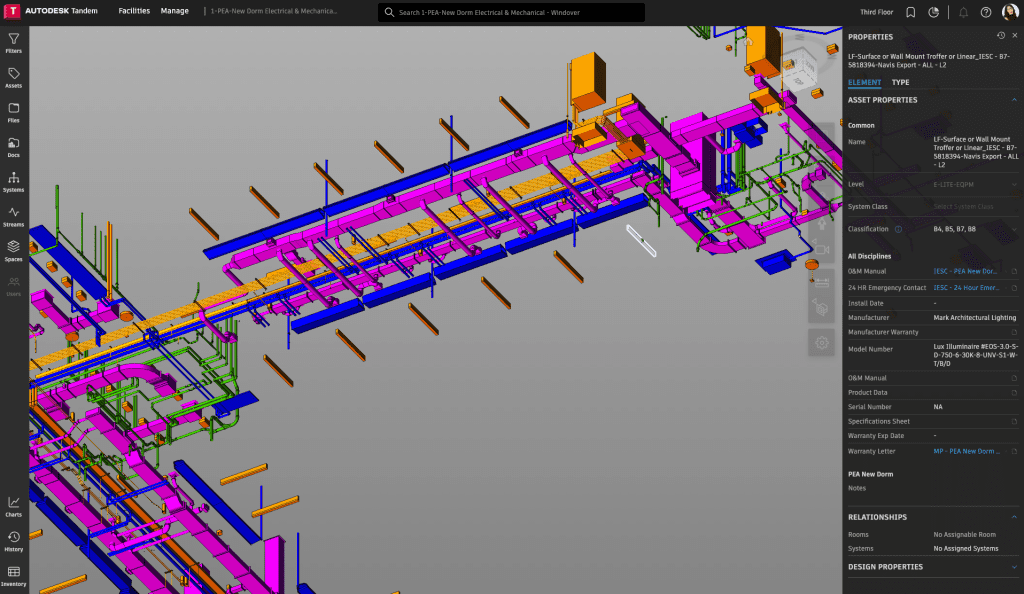
Looking towards the future
Tandem’s integration with IoT sensors will enable future predictive maintenance workflows, allowing the team to foresee issues before they escalate. The next step in the school’s digital twin journey is to integrate the sensors to better understand the building systems, operate more sustainably, and monitor how students and staff use their facilities. “I’m looking forward to integrating IoT sensors into the Tandem model,” Curtis said. “It’s going to be a great thing to see what’s happening live in our buildings and to be able to predict if something starts to go wrong before it happens.”
Moving forward, Phillips Exeter Academy plans to make the digital twin a standard practice across all their buildings, new and old. While the transition will take time through a scan to BIM to twin process, they look forward to having digitized facilities management for the complete lifecycle of their buildings and believe they will truly leverage the new tech even more in the next five, ten and even twenty years.
The Academy’s advice for other institutions
As word spread about Tandem’s success at Phillips Exeter Academy, Curtis believes it was a blueprint for the future of facilities management. “Any school that has a complex system that they’re maintaining, anything where it’s difficult to see all the parts of your system, a digital twin like Tandem is going to be the future,” he predicted. “I think that it should be something someone can embrace and start to use. Tandem will lead the way into the future of maintaining facilities easier with better information.”
Is your firm ready to stop wasting time looking for asset documentation? Learn more about digital twin technology and take the first step towards digitizing your workflow today. Take the digital twin assessment here.
More resources
Discover more articles, webinars, and whitepapers. Here are a few we think could be of interest.