Constructing tomorrow:
In the fast-evolving world of digital engineering and construction, leveraging advanced technologies to enhance operational efficiency is critical. Dura Vermeer, a leading Dutch construction company, has faced this challenge head on by using Autodesk Tandem to integrate digital twins into the company’s workflow. Mart Morsinkhof, BIM Coordinator at Dura Vermeer, recently shared how his company used Tandem to transform operations and building management.
Background and objectives
Dura Vermeer, a family business with more than 3,400 employees and annual revenue of 1.9 billion euros, has long emphasized safety, reliability, quality, and innovation. With divisions in infrastructure, real estate, mechanical and electrical engineering, the company sought to enhance its operations using digital twins. The primary objective was to connect near real-time data from their installations with their BIM models to gain deeper insights and to improve building performance.
“We wanted to connect real-time data to our 3D model to monitor our office installations and gain insights into their behavior,” Morsinkhof explained. “Our goal was to achieve predictive maintenance with minimal manual work.”
Azure digital twin: implementation and challenges
The journey began with the company’s office building in Utrecht, known as the Dura Vermeer Inspiration Center (DVIC). The DVIC had a detailed 3D model as well as data from the BRControls stored in Azure Event Hub, which they would connect to Autodesk Tandem to create a digital twin with near real-time data.
However, several challenges surfaced during the implementation:
- Data storage and integration: The data was stored in Azure Event Hub, which retains it for only one day. This required automatically creating a mapping table to connect the near real-time data with the 3D model.
- Minimizing manual configuration: Manual configuration was impractical because thousands of data points needed to be connected. To streamline the process, automation was essential.
- Developing custom tools: Custom tools were required to handle data transfer from Azure Event Hub to Autodesk Tandem and to automate the creation of data streams.
To meet these challenges, Morsinkhof’s team developed a two-pronged solution involving tools for both Azure and Tandem. “We created a mapping table to fit the data into the 3D model and developed a function app to manage data in the Azure Event Hub,” he said. “On the Tandem side, we automated the creation of data streams using the API.”
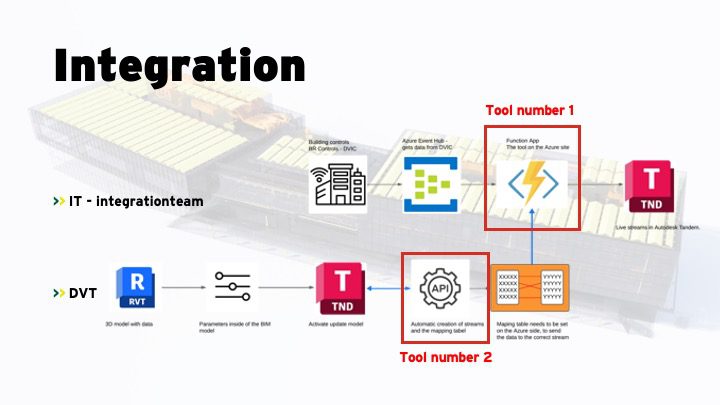
The Tandem – Azure digital twin: achievements and benefits
Despite the challenges, Dura Vermeer successfully connected near real-time data to its BIM model, achieving several benefits:
- Near real-time monitoring: The integration allows continuous monitoring of the building’s systems. For instance, they identified an issue with a malfunctioning fan operating in a small room, causing it to overheat. Real-time data pinpointed the problem, leading to prompt corrective action.
- Optimizing building performance: Insights gained from monitoring have allowed Dura Vermeer to maximize its building’s performance. “We discovered that turning off installations over the weekend was leading to higher energy consumption,” Morsinkhof said. “Now, we can adjust operations to prevent this.”
- Predictive maintenance: With near real-time data, Dura Vermeer is moving toward predictive maintenance, identifying potential issues before they escalate. Leveraging thresholds and charts inside Autodesk Tandem, Dura Vermeer can quickly analyze its historical data and track patterns of how its building systems are operating within defined tolerances. The upshot is that its customers can make informed decisions leading to preventive maintenance.
- Single source of truth: The integration has created a comprehensive data repository, ensuring that all building information is easily accessible and updatable.
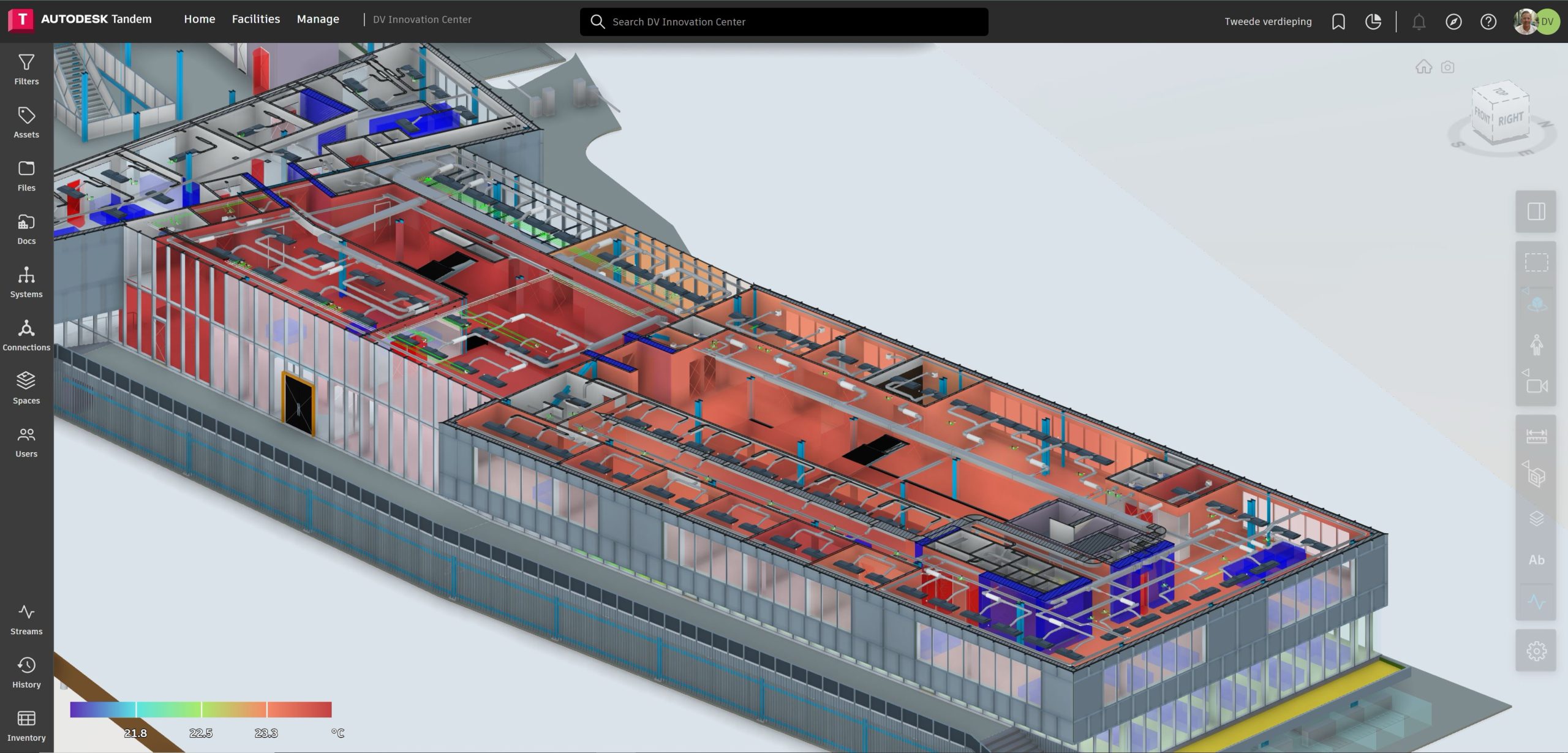
Looking towards the future: Wider use and more automation
So, what’s next? Dura Vermeer aims to automate its processes further and widen the use of digital twins across more projects. It is also exploring ways to increase data-driven engineering, which would improve future project designs based on real-world performance data.
Moreover, Dura Vermeer is exploring the possibilities to introduce this solution to the market. The company sees significant potential in offering a service that provides real-time monitoring and predictive maintenance based on integrated BIM and digital twins technology.
Combining real-time data and BIM
Dura Vermeer’s success story with Autodesk Tandem exemplifies the power of integrating BIM and digital twins in construction. Operational improvements were made possible by connecting near real-time data with 3D models — from real-time monitoring and predictive maintenance to optimized building performance and a unified data repository.
For more details on the impact of digital twins, learn more from Dura Vermeer’s experience during their May 2024 webinar or start your digital twin journey for free today.
More resources
Discover more articles, webinars, and whitepapers. Here are a few we think could be of interest.