The Value of Autodesk Tandem for AEC Firms
The Challenge for AEC Firms
With the growing trend of building owners moving away from the traditional design-bid-build process in favor of a direct design-build partnership, it is increasingly critical that architecture, engineering, and construction (AEC) firms differentiate themselves to garner trust and cooperation at the earliest stages of an engagement. This is easily achievable by presenting owners with clear value propositions during three stages of the building lifecycle: upfront specification and design, construction, and post-handover and facilities operations.
During the first stage of early specification, AEC firms need to demonstrate how the owner can be involved in the design process, specifying their operational requirements, with a focus on future operational readiness. When owners can clearly see how up-front planning and preparation will directly affect future costs and revenues associated with building maintenance and operation, they will be incentivized to choose AEC firms that can accurately and readily produce this data.
During the second stage, when the actual building structure is being transformed from concept to reality, owners must be certain that the numerous stakeholders in the process are working together in stride at the highest possible efficiency. To reduce the delay from handover to operational readiness, owners must have the trust and the confidence that all the asset and equipment data is correctly populated in the operational system as they are procured and installed in the facility. This directly controls the overall project budget and likelihood of meeting any proposed schedule and reduces the time for operational readiness. Any AEC firm that can demonstrate an ability to do this on past projects and detail plans to do it on a potential project stands the greatest chance of successful partnerships.
Lastly, during the third stage, when a completed project is handed over to the owner and their operations team, AEC firms must strive to ensure that their clients hit the ground running. The status quo suggests that most owners don’t receive their building operations data until after about 12-18 months of actual use, and some owners never truly reach a meaningful understanding of this critical data. This is due to large, overwhelming volume and variety of the data in various formats. Another major reason is due to lack of trust in the data. AEC firms that can successfully set up their clients for operational readiness on day one – and can demonstrate how they will continue to enhance the owner’s profitability after handover through on-going services – will undoubtedly rise to the top of their competition. Autodesk Tandem is specifically designed to help AEC firms gain a competitive edge by tackling these three stages of development. Adding Autodesk Tandem into existing building information modeling (BIM) workflows guarantees that they will be one step ahead of the game, effectively distinguishing their services from their rivals.
What is Autodesk Tandem?
In the most basic terms, Autodesk Tandem is a digital twin solution that transforms the built asset lifecycle to start digital, stay digital, and deliver digital by creating a digital thread through the different phases of the built asset lifecycle (i.e., design, build, and operate phases). Leveraging industry-standard BIM data, Autodesk Tandem acts as a central arbiter of asset information for AEC firms, facility managers, and owners to turn fragmented data into business intelligence.
Autodesk Tandem is entirely cloud-based, offering its broad user base accessible, contextual, and insightful data. This allows the various stakeholders of a built asset to stop managing individual files and documents, and instead focus on the process to specify, capture, and verify their tasks while simultaneously tracking every change.
Core Concepts Behind Tandem
Fundamentally, Autodesk Tandem relies on BIM to create an exact replica of a building asset known as a digital twin. This digital replica evolves in synchrony with the actual building, from initial concept and design to the as-built manifestation, and then even further throughout its maintenance and renovation cycles.
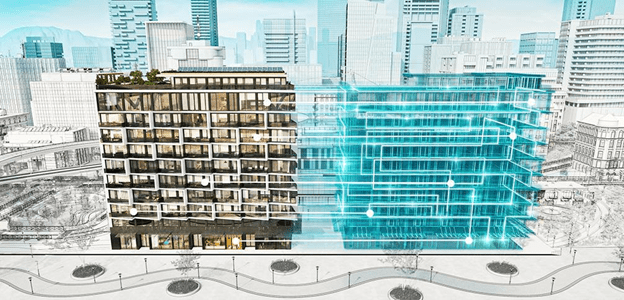
The process begins with architects and engineers who create the initial digital designs, often in Autodesk Revit or a similar BIM-based design software. At this point, the digital twin is born as a virtual digital twin, and as the construction team brings the physical structure into existence in the real world, it evolves into a physical digital twin.
Autodesk Tandem is a digital twin that evolves and can be modified with exact asset information. Upon completion of construction, the physical building and the digital twin are handed over to an operations and facility management team. Using Autodesk Tandem, they will be able to monitor the health and functioning of the structure using connected sensors, maintenance computers, and intelligent building equipment.
The AEC Firm’s Advantage with Tandem
With Autodesk Tandem, AEC firms can improve and expand their business interactions based on experience and specialization – a boon for client referrals and future projects, particularly if considering design, build, or operate projects. This specialization is garnered by integrating the digital twin concept into every aspect of the building life-cycle. Different teams ranging from the engineers and architects to the owners and contractors are able to work within a common tool suite.
With Tandem, AEC firms can help overcome traditional handover problems by delivering digital twins to clients as part of the completed work asset. The extra effort required to properly build the twin can be leveraged by promoting it as an additional, specialized service that adds significant value to future building operations.
After the handover, digital twins still need to be maintained. As facilities evolve, assets may need to be replaced or upgraded, and new systems can be installed. By proposing to keep the digital twin updated on behalf of a client, AEC firms can cultivate an ongoing relationship with owners and facility managers opening new revenue streams through multi-year maintenance contracts.
By starting with the end in mind, Autodesk Tandem sets your clients up for long-term operational success. Customers can specify the data they want to end up with from the beginning. Project teams can then use Autodesk Tandem as a well-structured foundation, layering on and coordinating data from new or existing systems. The result is a digital replica with all the information a client needs for operational performance and insights, right at their fingertips.
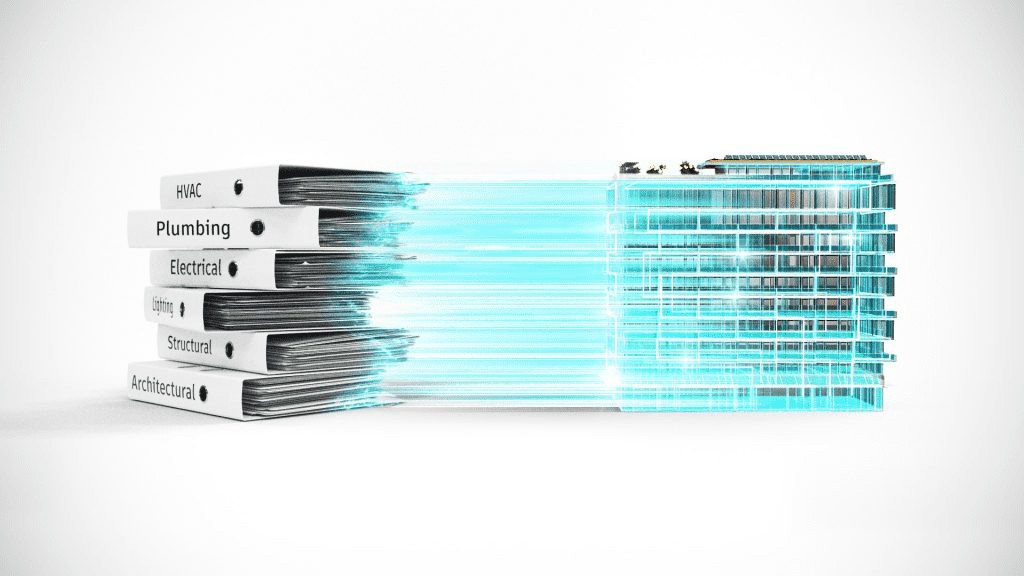
The Future is Tandem
Autodesk Tandem provides the underlying structure that underpins the practical value of digital twins. On top of this structure, a variety of tools will be created and then evolve with the mainstream industry adoption of digital twins. Today, Autodesk Tandem is focused on creating the most descriptive, useful digital twin from the AEC’s perspective. Upcoming features will focus on integrating facility monitoring, and the near future will offer the potential to use existing twins to optimize a building portfolio.
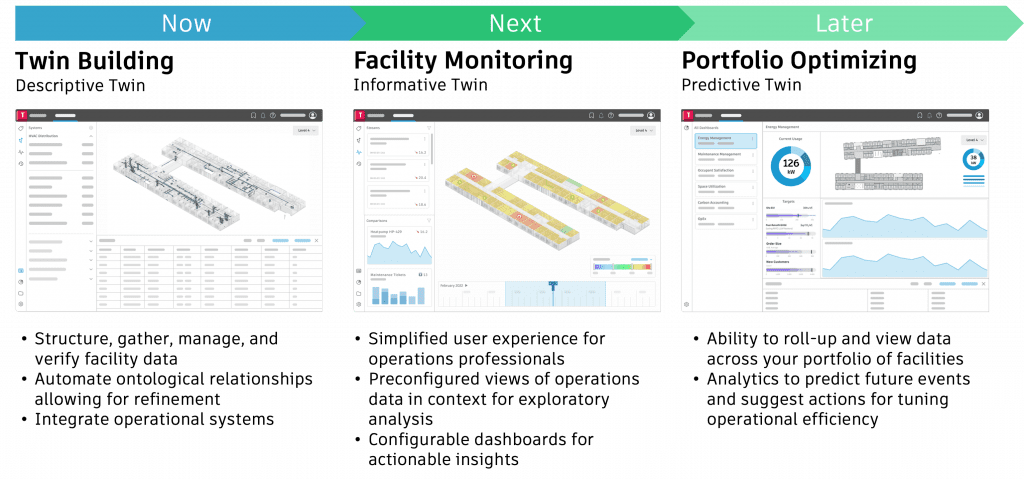
In addition to the base feature set, Autodesk Tandem will offer comprehensive APIs in several contexts to help developers customize and extend these capabilities. Combined with open data standards, there is no limit to how Autodesk Tandem can be integrated into existing operational systems or used to support custom workflows and applications.
To learn more, visit https://intandem.autodesk.com/business-values/
More resources
Discover more articles, webinars, and whitepapers. Here are a few we think could be of interest.