Digital twins offer a Competitive Advantage
Imagine finding a new service that solves your client’s pain points, extends your value, fits into your already established workflows, and provides your firm with a competitive advantage during the proposal process. While it may sound too good to be true, contractors across the globe are accomplishing this by offering their clients digital twins. Through introducing digital twins to building operators, AEC firms are adding value that’s been missing and helping their clients solve new problems — from extending their existing relationship, to filling the gap between the handover process, and to long setup times in making the facility operational – these firms are getting called back to implement digital twins. They have a seat at the table to problem-solve diverse operational issues and help their clients work towards operating more sustainable buildings.
What is a digital twin?
A digital twin is a data-rich, 3D interactive model that mirrors its built asset in appearance and substance. Its value comes from how it centralizes and contextualizes data for the building’s lifecycle. These comprehensive virtual replicas connect real-life assets with their IT/OT data, giving users holistic and granular visibility of the information that matters most to them.
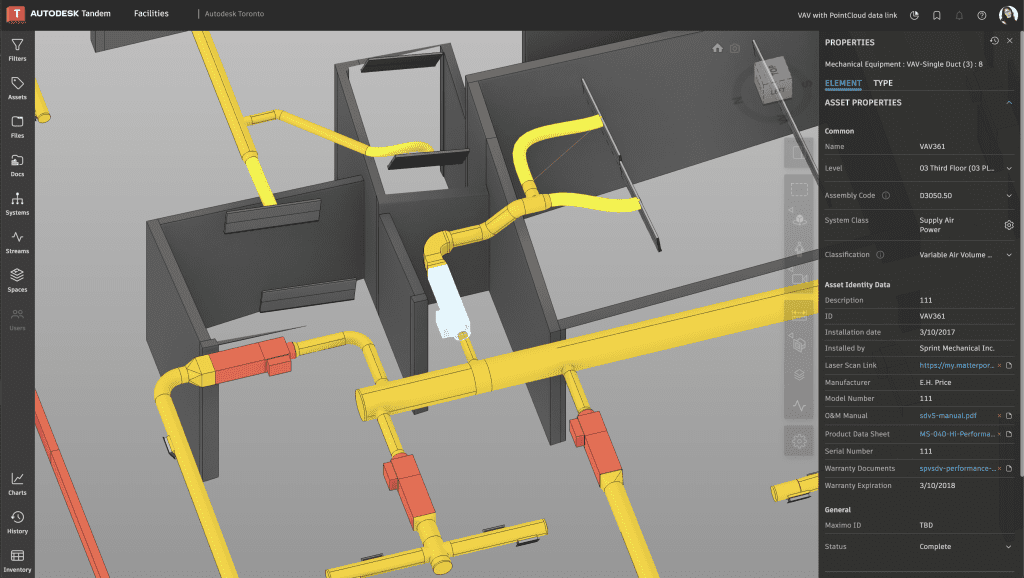
Extend your value by solving new problems for your clients.
The building lifecycle is highly fragmented, building operations are siloed, and facility managers have an extensive wish list for data that could help them operate facilities more efficiently. AEC firms can extend their value by leveraging existing BIM data and expertise to help owners and operators solve their data issues and work more effectively. Here are a few examples of how AEC can leverage tech to extend their value:
1. Digitizing the handover process to eliminate facility management data loss.
From design through construction, tons of data is generated by AEC firms, but 95.5% of all data captured and created in the design-build process gets lost. To shed light on why this is so problematic, a 2023 survey from the IFMA IT community found that 74.4% of participants deemed that asset lifecycle data was “very important” to successful facilities management – yet that data is either being lost or delivered in a way that might not be usable to building operators.
To fix the data loss at construction handover and to put data in a usable format, AEC firms are building digital twins. The foundation of these twins includes BIM models and structuring design, construction, and commissioning data in a format that is usable beyond operations. That means every asset in the building is mirrored in the twin and can be tagged with all the data necessary to maintain it, including owner’s manuals, installation dates, warranties and more. The digital twin provides owners and operators with more knowledge about what assets they have, quantities, and locations throughout their facility.
Not only does this digitized process help owners and operators, but building a digital twin eases the dreaded handover process by streamlining the workflow. Digital twins refine the construction handover process, especially for multi-year projects, since they begin in the design and build phases of the project lifecycle. Project teams suffer from employee turnover, project managers moving on to their next projects—and most often, final payments are tied to handover completion. All these factors, along with the fragmented nature of project delivery, lead to turnover in haste. With Tandem, project teams can “close as they go,” ensuring the handover data is aligned with the owner-operator’s specifications and in the structured format, which is valuable and consumable for facility operations.
2. Break down data siloes and reduce fragmented data.
Due to the handover gap, facility managers use siloed and fragmented data to maintain and operate their buildings. A 2023 survey from the IFMA IT community found that 72% of facility managers use spreadsheets to manage their assets. In addition, 68% used CMMS, and 46% used email. These mediums cause a disjointed workflow with prominent data silos.
Digital twins are data repositories, providing a hub for facility management data throughout the lifecycle of a building. Every piece of data about an asset can reside in the twin, and the options are customizable for the needs of each owner. Beyond being a data repository, the twin breaks down silos by being able to centralize data, simplifying the end-user’s workflow.
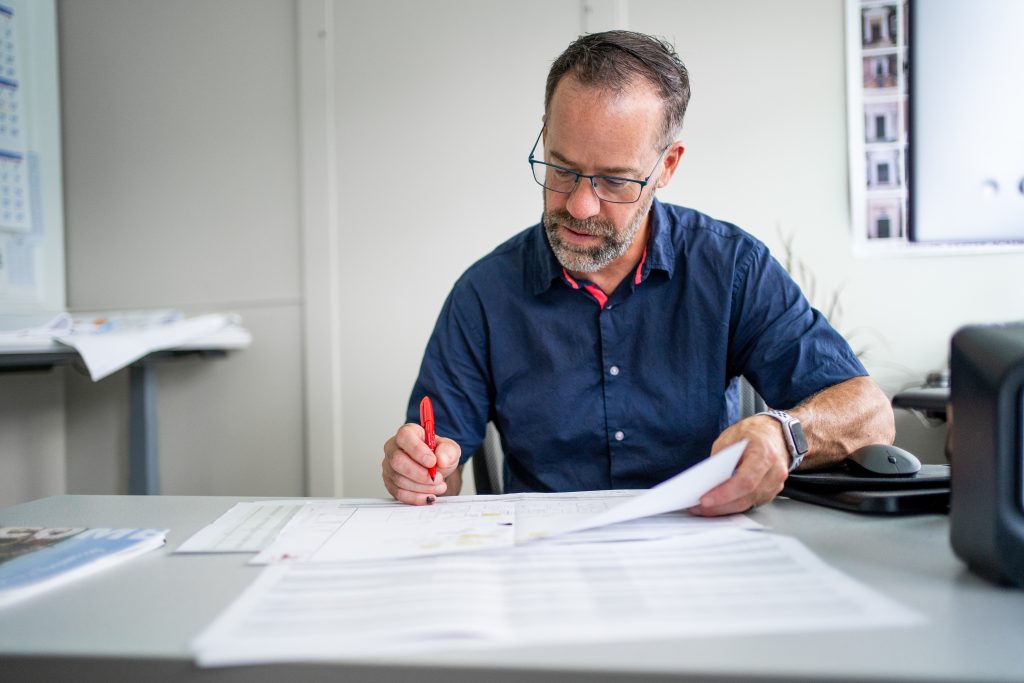
3. Expand capabilities with insightful operations.
74.4% of survey participants in the IFMA IT study claimed that current condition data was critical to successful facilities management. In that same study, 52.5% of participants said they planned to invest in IoT sensors and energy monitoring systems in the next 12 months.
When connecting IoT sensor data to a digital twin, you’re helping clients visualize data in context of their buildings. Autodesk Tandem houses IoT sensor data and provides graphs of historic trends to contextualize the data. By applying heatmaps to building spaces and systems, these data points highlight what matters most.
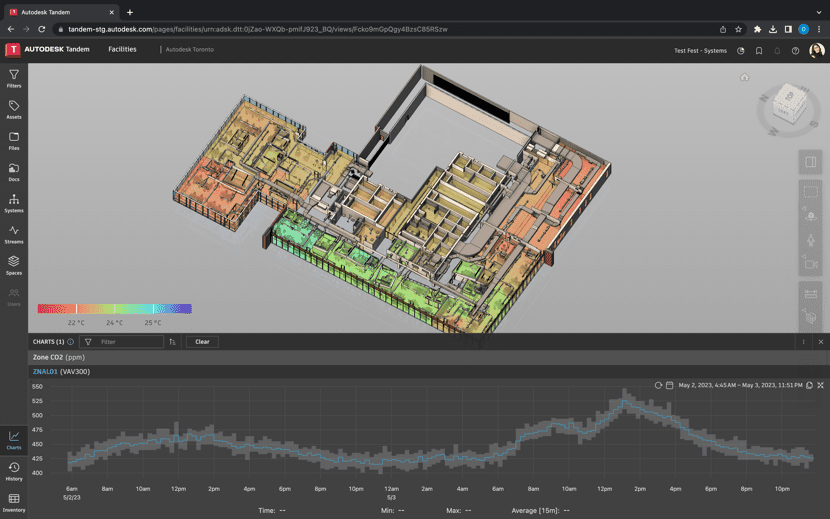
4. Extending service to operations.
Most general contractors in the United States have contractual warranty obligations for one to two years post-handover. For scopes like waterproofing, that warranty can extend up to 20 years. Having a digital twin of the new build is immensely valuable for contractors looking to extend the value of their services beyond construction, whether responding to warranty calls, providing quality assurance on the built asset, or building a new service line. Similarly, for architects and engineers, a digital twin can provide valuable performance feedback on decisions made during the design-engineering process. For owners and operators, this means having partners that better understand their buildings, quicker maintenance, and less downtime.
How to position the digital twin.
1. Run a pilot on active projects.
Test out building digital twins for your clients and recognize the value through running a pilot project for free. AEC firms are testing the capabilities and delivering digital twins for their clients at project handover. By introducing the concept to their clients, they are gaining a better understanding of how to leverage the technology in the future. For many AEC firms, this offers quick wins with their customers, as their clients see immediate value in the digitized handover and discover new possibilities with the unlocked data available in the digital twin. Delivering a digital twin is a simple way to add value— with a small lift in effort, time, and minimal risk — resulting in a positive engagement with your customers.
2. Educate your clients through your RFPs.
Depending on the RFP, there may be an opportunity to share information on the pain points building managers suffer from a typical project handover. Like, how your team plans to fix the data loss that currently exists and extends your firm’s BIM expertise in a format that non-technical users can gain value from. Digital twin technology will benefit facility managers and building operators by handing over a facility that is operationally ready on day one. The digital twin will also unlock longer-term benefits by helping save money with predictive maintenance, operating their buildings more sustainably, working more efficiently, and helping them better understand their assets, quantities, locations, and more.
3. Start having conversations with building operators.
Clients want their buildings constructed on time, on budget, and without rework. Yet, how often are conversations happening about efficiently and sustainably operating those buildings over the long haul? How much time are they losing looking for data on their assets? AEC firms might be shocked at how they can quickly help their client’s day-to-day jobs throughout the lifecycle of the building by digitizing the handover data to building operators. These conversations allow you to identify how to position handover with a digital twin for various building types. It doesn’t stop there, but there’s potential to extend relationships into operation stages of the building lifecycle, opening the door for contractors to begin new business opportunities in facilities management.
How building digital twins fits into your team’s workflow.
Digital twin creation is a natural extension of the workflow already in place for AEC firms with established BIM and VDC practices. The basis of a digital twin is created with BIM data, which is easily generated by uploading Revit and IFC files. The data associated with a descriptive twin is captured and verified throughout design, build, commissioning, and even the rest of the building lifecycle. Autodesk Tandem Senior Product Manager Tim Kelly explains, “Twin building should coexist with the design and construction processes, serving as a conduit for managing essential data requirements and ensuring the facility is delivered as intended.”
Offering a digital twin to your clientele is low-hanging fruit to gaining a competitive advantage. It will extend value to building operators and facility managers for years to come—and it is a repeatable process that already complements vital BIM and VDC workflows. Kickstart your competitive advantage and pilot your first digital twin project for free now.
More resources
Discover more articles, webinars, and whitepapers. Here are a few we think could be of interest.