Twinning Autodesk
How Autodesk is expanding the use of Tandem
It’s not every day that a software company has a use case internally for the product they develop. At Autodesk, multiple teams across various organizations have found valuable use for the digital twin solution Autodesk Tandem. Building a twin of Autodesk’s Toronto office has served as a testbed for the Tandem team. It is a real-world proof of concept for each new feature the developers create, and an engaging live demo to educate architects, engineers, contractors, building owners, and operators on what is possible. This digital twin has inspired other teams across Autodesk to expand the use of Tandem internally and create twins of other Autodesk facilities – from Tech Centers with manufacturing equipment to a gallery to track engagement with exhibitions.
What is a digital twin?
A digital twin is a dynamic digital replica of a built facility, that centralizes and contextualizes data, including connections to real-life operational data. Autodesk Tandem is a digital twin solution for the architecture, engineering, construction, facilities management, owner, and operator industries.
The Toronto office digital twin:
If a digital twin is a replica of a real asset, the Tandem team needed a real facility to twin for testing purposes – cue the Toronto office. Autodesk inhabits two floors of the west tower at the MaRS Discovery District. Since August 2022, the team has been iterating on the twin of the building, testing new functionality, and using the site as the primary product demo.
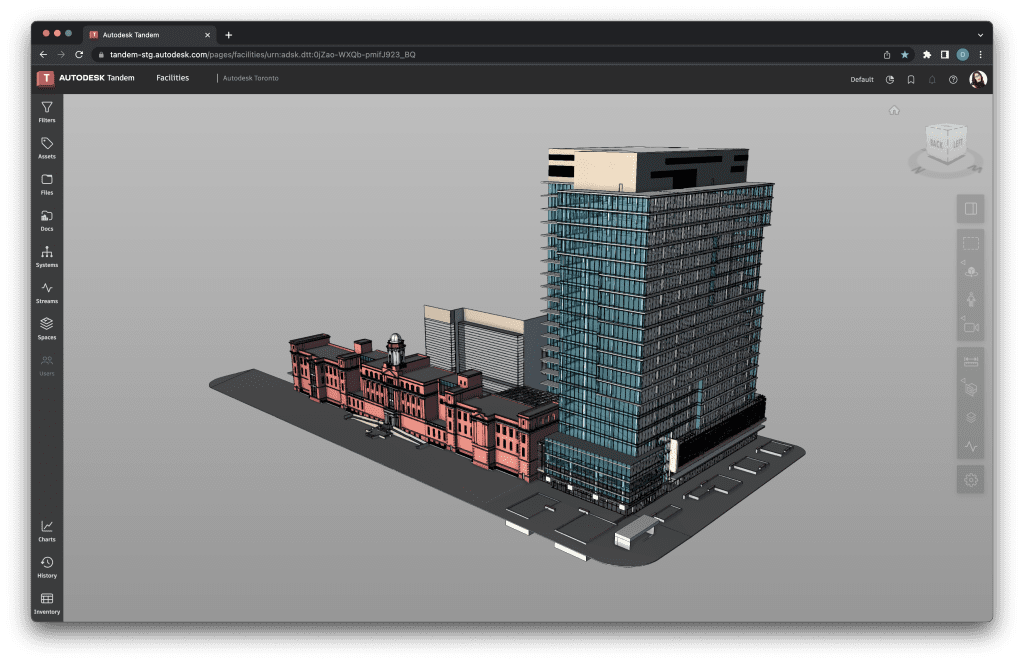
(An image of the façade of the MaRS Discovery District inside Autodesk Tandem)
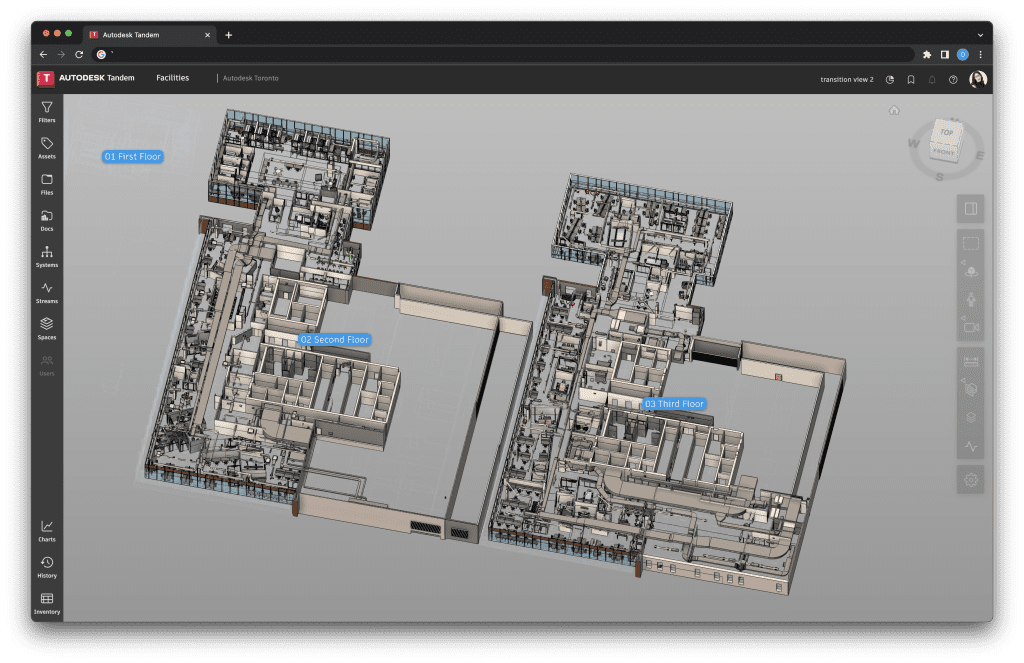
(An image of the two floors Autodesk occupies)
Consolidating facility maintenance data for the Toronto Office:
The Toronto office started as Tandem’s flagship testbed, comprised of architectural, structural, and MEP models, and now hosts a variety of facility management data for the MEP (mechanical, electrical, and plumbing) systems, including operation and maintenance manuals, warranties, install dates, and even quick links to 360 views of the spaces in Matterport scans. Despite the Toronto office’s digital twin being generated for testing and proof of concept only, this sample site demonstrated how storing facility maintenance data inside Tandem could reduce the time to find the appropriate data, which may be buried in documents in folders or that was never cataloged outside the design deliverable. Tandem would make it quick and easy to find valuable data when it’s needed. In conjunction with the 3D replica of the building, it would provide contextual awareness, simplifying the navigation to specific assets.
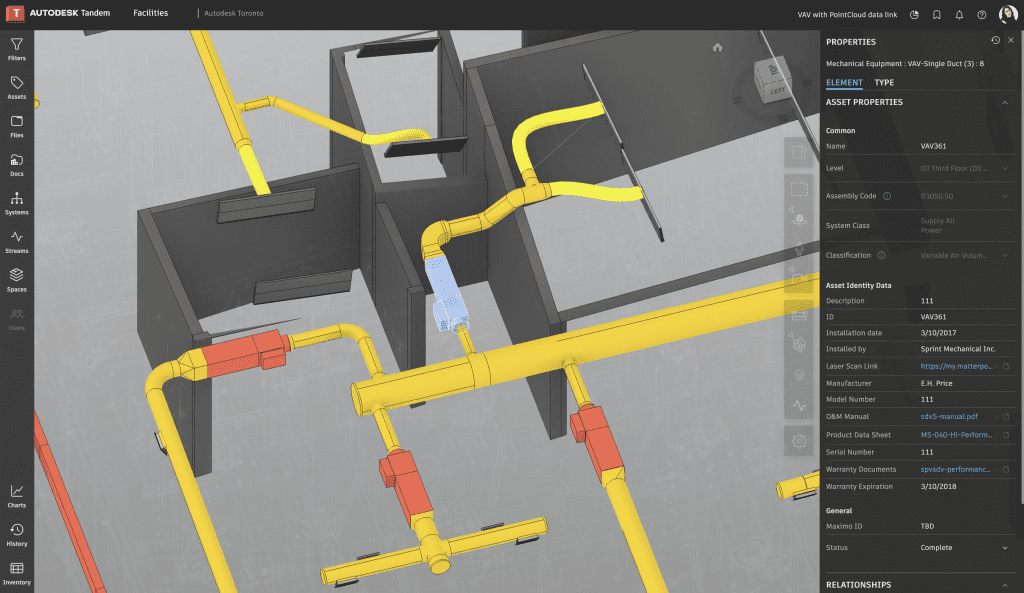
(An image of a VAV Box on a supply air duct selected in Autodesk Tandem displaying the assets manufacturer, model number, O&M manual, serial number, warranty expiration, as well as a direct link to the asset in the Matterport scan).
Insightful operations capabilities demonstrated with the Toronto facility:
The Autodesk team has tapped into 82 different connections to VAV (variable air volume) and FCU (fan coil unit) devices managing airflow, providing the team with 230 live streams of temperature, humidity, CO2, and flow rate throughout two floors of the building. Since August 2022, these connections poll the Building Management System every 1 minute, providing a continuous flow of data into Autodesk Tandem. Configurable heat maps put this data in context to the building, while simple-to-understand time series charts are available to track the HVAC performance.
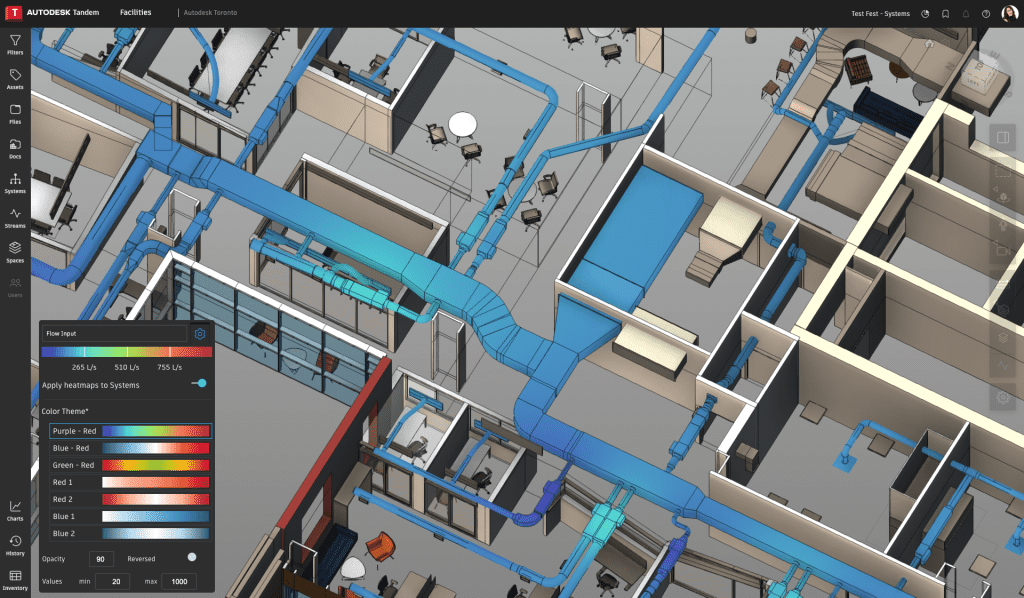
(An image of the HVAC system with a heatmap of the flow input being applied to the system)
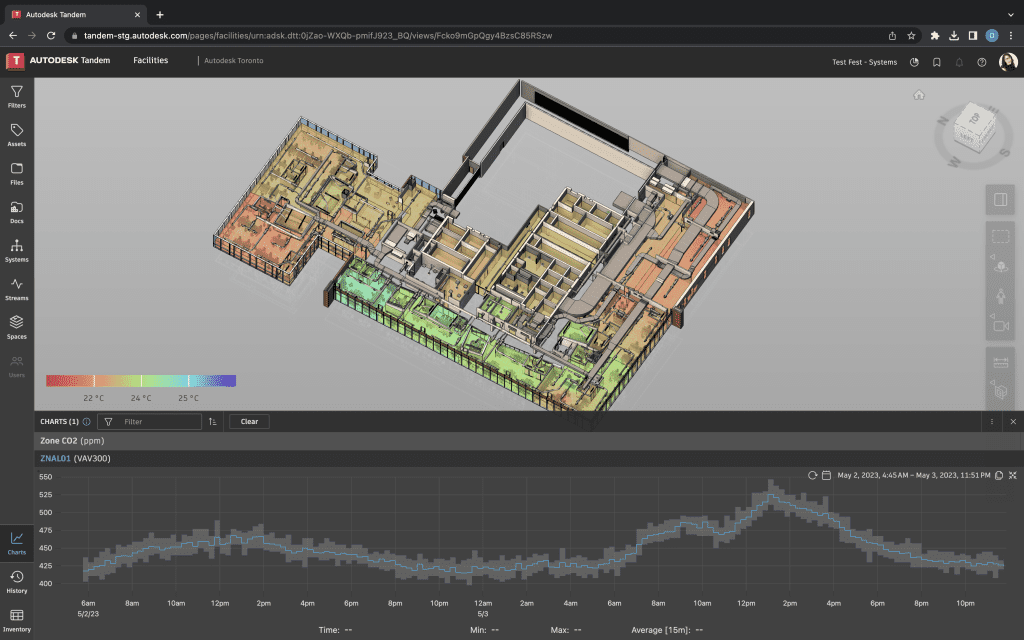
(An image of the Tandem UI with the Toronto Office illustrating a heat map of CO2 data applied to spaces on a floor of the building and a chart demonstrating that data over time).
The Autodesk Toronto office demonstrates the power of digital twin technologies for understanding building performance and achieving operational excellence. This testbed site has collected near real-time data that can inform decisions to tune or retrofit the building’s systems. The results have excited facility managers, workplace technology teams, and even gallery managers within Autodesk to apply its many capabilities to their unique use cases.
For a deeper dive into how Autodesk is using the digital twin of the Toronto office watch this video:
What value is Autodesk seeing from using Tandem?
Jessica Smith, former Autodesk Facility Coordinator, and current Support Program Specialist for Autodesk Tandem, explains, “Tandem is something I wish I had when I was working in facilities. The easy access to data, asset location, and history would have saved hours, not to mention the time spent on a ladder trying to find something. Now with Streams, Tandem has taken one challenge owners/operators face and put it into a picture, that is worth a thousand words with the potential to save owners just as much in spending.”
Expanding Tandem beyond the Autodesk Toronto Office
In 2023 Autodesk plans to expand the use of Tandem beyond the Toronto facility and into other offices globally. Movement is underway with the Birmingham and Boston Tech Centers, and the San Francisco gallery. Each office’s facility management teams have seen the value in Tandem and considered use cases unique to their facilities.
The Autodesk Boston Tech Center & Office:
The Boston Technology Center has gained interest from multiple stakeholders – in facility maintenance and within the team overseeing the maintenance and upkeep of manufacturing equipment.
For facility management at the Boston office:
“While Tandem can show us granular data, it also would be ideal for an overall high-level picture of what’s going on in the facility – providing our team with information on potential issues from lighting, heat, temperature, occupancy, and to see where the issues are located.” Steve Boulas, Facility Manager of the Boston Autodesk office, is at the beginning stages of implementing a digital twin after seeing it in action for the Toronto facility. His team is eager to use Tandem to aggregate data from their BMS, mechanical systems, occupancy sensors, and other tools. He explains, “We would be using Tandem every day – two to three times per day, especially first thing in the morning to do a quick high-level check of systems, who’s there, and what rooms are occupied. This would help us save time avoid checking every room and prioritize walkthroughs.”
For overseeing manufacturing at the Boston Tech Center:
Beyond the basics of facility monitoring the Boston office has two floors of wood, mechanical, and 3D print shops – all with machinery that the team could better maintain and operate for operational, financial, and safety reasons. “We currently have critical infrastructure located on the second floor. The room is required to maintain negative air pressure to be safe to enter the room. We do have safety measures (alarms) in place that give us insight to fan failure, but it would be enhanced if we had a way to see real time usage, occupancy, and more insight into the operation of the room remotely at a snapshot.”
“The humidity and temperature really affect the equipment and the manufacturing of parts,” explains Joe Aronis, the Technology Centers Workshop Manager for Boston. “You want to maintain a certain temperature, and if there’s a large deviation in temperature, that’s alarming because that will affect the tolerances. A lot of humidity with additive manufacturing will affect the print quality of your parts, spring failures, and more. So having a nice view and dashboard of the actual physical conditions of your sites is huge.”
Jessica Smith elaborated on Steve and Joe’s needs, “If a machine breaks, having the historical data of the payload and temperature readings on the equipment would help problem-solve a little faster. This would also help with the life expectancy of the machine and then maintenance, like a car, we’d know the mileage and when to go in for an oil change – some of the machines in the Boston office have very similar indicators, and every so many months need maintenance to happen. Beyond the value of better maintenance of machinery, collecting this data could also help with capital planning, so Autodesk can better build out future spaces through a better understanding of machine usage.
The Birmingham Tech Center:
We’ve currently begun a process of scan to BIM to twin with the Birmingham office. The building has been laser scanned, and with the help of PointFuse the team is converting those into mesh 3D models, then into Revit models to use in Tandem, illustrating the workflow for many pre-built facilities that want a digital twin. From there, the Birmingham facility managers look forward to tracking data on machinery similar to the Boston office.
Nick Hill, Autodesk Director of Technology Consulting at the Birmingham site, explains, “The Autodesk Birmingham (UK) office and Technology Center is not too dissimilar to most building stock. It is a 1980’s build with little to no data; whether that is the original “blueprints,” the latest drawings depicting the HVAC and MEP infrastructure, or digital plant and operational data. The little data we have all lives in isolation in different formats. To make matters more complex, the facility is a Technology Center that has a vast array of state-of-the-art equipment and technologies, all using different file formats and communication protocols. Understanding the issue with all the different file types (or lack of data) better illustrates why a single common solution to visualize and contextualize the physical spaces, asset data, and data streams is critical to improving operational efficiencies across the site. These operation efficiencies span multiple use cases: how employees and visitors use the facility, how the Technology Centers operates, how the facility is maintained, and how these spaces can be repurposed and put to better use.”
The Birmingham project is an open initiative to create an extensible digital twin, one which will be continually updated and maintained to serve as a long-term research and collaboration project that will enable exploration into the performance and optimization of facilities and operations, all with the expressed aim of a drive towards scope 1 & 2 net zero.
Catch up with the current progress of the Birmingham Tech Center Digital twin here.
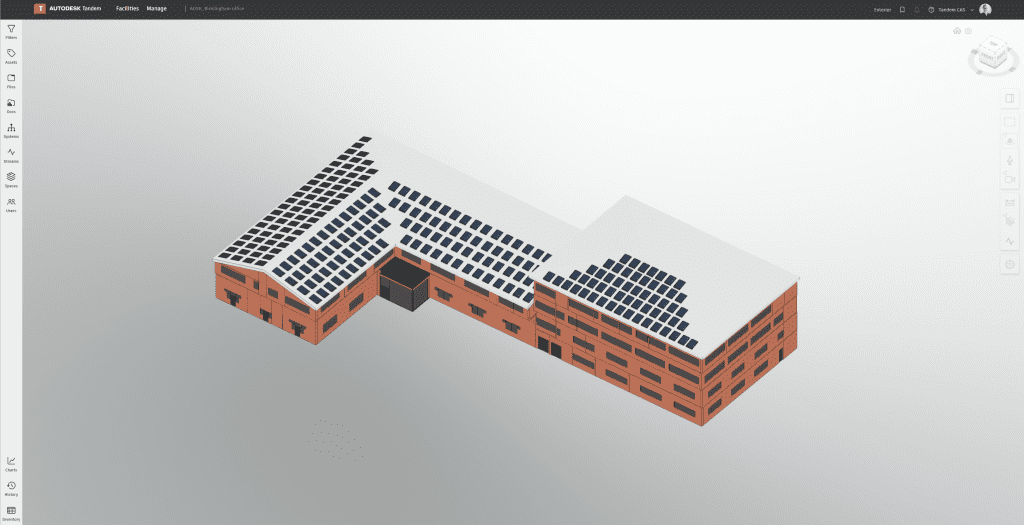
(The Birmingham Tech Center modeled and imported inside Autodesk Tandem.)
The San Francisco office:
Autodesk’s San Fransisco office gallery will also be getting a digital twin. The gallery will be collecting sensor data tracking how visitors explore the space and interact with the exhibits. This will help the curators create more effective exhibits but using heatmaps in Tandem to understand interaction and patterns from visitors. Not to mention – the digital twin of the San Fransisco gallery will be up for display in the gallery itself!
Join the digital transformation and benefit from a digital twin
Autodesk Tandem is aggregating data from multiple sources with the added value of the 3D replica providing contextual information, supplying owners, operators, and facility managers with insightful contextual data and leading them towards operational excellence. Join the digital transformation and try Autodesk Tandem for free today.
We’re here to support you in harnessing the power of digital twins for your business. Understanding the technology, its applicability, and your readiness to adapt to it is pivotal. That’s why we’ve crafted a comprehensive Digital Twin Assessment Readiness. It’s designed to provide you with an in-depth understanding of your readiness, highlighting potential compatibility with the integration of digital twins into your workflows. Start your journey now by accessing the Digital Twin Readiness Assessment.
More resources
Discover more articles, webinars, and whitepapers. Here are a few we think could be of interest.